ACC: Polyurethanes now material of choice for sports shoes
Lou Reade
19-Sep-2014
Once upon a time, you could have sports shoes in any colour you fancied… as long as you liked black (or occasionally brown). Now, you really can get any colour you like – and it’s largely because athletic shoes are made with polyurethane (PU) rather than real leather.
PU, in its many forms, can be used to make just about any part of a sports shoe – from the foamed midsole on a running shoe to the hard studs of a moulded football boot. It is often the material of choice for the new generation of vibrantly coloured products.
“The use of thermoplastic polyurethane (TPU) has grown and grown, whether it’s for trim, decoration or studs,” says Craig Roberts, global marketing and technology director at Huntsman TPU.
|
---|
Rex Features The use of polyurethane in footwear has come on in leaps and bounds in recent years |
The company extended its Avalon 95 series of TPUs, with two grades specifically aimed at sports shoes. Its ABU grade offers high resistance to ultraviolet (UV) light, while its AHT grade is ideal for moulding transparent parts.
“Transparency is a trend that’s come and gone over the years,” says Roberts. “This time, the required level of transparency is higher than ever – and it must be stable enough to avoid yellowing.”
Part of the challenge was to develop a stabiliser that protected against UV light but did not affect transparency, in parts thicker than 6mm. At the same time, the material needed to maintain physical properties such as flexibility. “It’s taken two years to develop,” he says.
The second grade, ABU, focuses on UV performance. It is a “workhorse” grade aimed mainly for use in football cleats.
“The UV resistance ensures that vibrant colours do not fade quickly,” he says.
Parts made from these grades stay pristine for longer than those made from those from competitors, he says.
In addition to these new grades, Huntsman is modifying existing materials for the sports shoe market. SmartLite is an expanded TPU technology that has previously been used in the “luxury casuals” market. The company is now looking to use it in the larger sports shoe sector.
“We’ve worked with some customers in Asia to push its density lower,” says Roberts.
He says that TPU growth is around 5%/year – of which footwear is the largest user. Huntsman is ready to capitalise on this, having opened a new 21,000 tonne/year TPU plant in Shanghai, China, earlier this year, putting it on a par with its two existing plants in Europe and North America.
“Before, we supplied to Asia from our plants in Germany and the US,” says Roberts.
ADHESIVES REMOVED
Klockner Desma of Achim, Germany, has developed a new concept for making sports shoes, which uses four separate PU components – and no adhesives.
Sports shoes must be built to include a variety of physical attributes, including grip, abrasion resistance and shock absorption. This is usually done by making different parts from different materials, then joining them together. Desma’s technique, called QuadWrap, allows it to incorporate many of these necessary physical attributes using only grades of PU.
“The complete shoe – sole and upper – is produced by PU casting and injection moulding,” says the company’s Karsten Stobener. “The PU layers of shoe are joined in the production process – avoiding any adhesives and VOCs [volatile organic compounds].”
|
|
---|
Kloeckner Desma PU is increasingly prevalent in footwear |
BASF BASF and adidas are making great strides |
Properties such as Shore hardness, colour and density are adjusted in-process for each PU layer – by varying the component mixing ratio, and by adding pigments and other additives in the mixing head of the injection moulding machine. Densities down to 0.2g/cubic centimetre (ccm) are achievable.
The process requires two moulds. In the first, the inner shoe structure is injected directly on to a textile sock. In the second mould, the outer sole is produced in parallel. The two parts are then brought together in the second mould, where injection of the midsole and outer upper layer joins all the components together and produces the final shoe. Excess material is cut away after demoulding.
IN FOAM FORM
QuadWrap includes a foamed PU that has a similar density to ethylene vinyl acetate (EVA). It is made by adding a blowing agent to the liquid PU in the mixing head of the injector.
“The midsoles have a density comparable to EVA, but with the excellent mechanical properties of PU,” he says.
Stobener says the technique could help to reduce costs by boosting manufacturing efficiency, and by focusing shoe production on a single machine: rather than being assembled from pre-made parts, the shoe is made directly from the four injected components on a rotary table injection moulding machine.
The company has designed and produced a sample QuadWrap trainer using the technique. “Due to its massively reduced dependence on labour costs, QuadWrap can be an excellent basis for shoe mass production close to consumer markets – even in high labour cost countries,” he says.
Last year, with great fanfare, adidas launched its Energy Boost running shoe – which relies on a new PU from BASF.
BASF says the material, called Infinergy, is the world’s first expanded TPU. The closed-cell particle foam is more springy than competitive materials, it says. Its “rebound height” (the amount by which it springs back) is 55% – exceeding other particle foams such as expanded polystyrene (EPS) (around 20%) and expanded polypropylene (EPP) (30%). This makes it ideal as a cushioning material for running shoes.
Gerd Manz, senior innovation director of global brands at adidas, says the material manages to combine softness and elasticity. “Previously, runners had to choose between hard, elastic competition shoes or a very soft training shoe offering a lot of cushioning,” he says.
After three years of working together, adidas and BASF combined these elements by specifying Infinergy into the midsole of the shoe.
The rebound characteristics of the material can be varied by altering the density, according to Martin Vallo, head of sales and technical service for footwear, BASF Polyurethanes.
“The formulation has a strong influence on properties, and we are constantly trying to improve them,” he says. “Also, processing parameters are influencing the performance of the material.”
He adds that development is continuing, and BASF is now supplying two different Infinergy grades to adidas for its Boost range. Adidas says it plans to use Infinergy in all sports shoes costing more than €100 ($132), as well as extending it to other products – ranging from basketball boots to snowboarding applications.
While Infinergy will not be seen on sports shoes from other manufacturers – due to an exclusivity agreement – that does not mean it is unavailable to other companies, for other applications. “For safety shoes, there is no exclusivity,” says Vallo.
In common with other suppliers, BASF believes that PU offers a way of cutting the production costs of sports shoes – by replacing several other materials (such as EVA), and its ability to be used in automated processes.
“We are actively developing PU systems for sports shoes based on Elastopan and Elastollan,” he says. “Our PU systems can support the sport footwear industry in their efforts to introduce automation processes – and help bring production of sports shoes back to Europe, or to where they are sold.”
The quest to manufacture sustainably – using fewer harmful chemicals, and less water and energy – has not escaped the sports shoe market.
Bayer MaterialScience has extended the scope of its water-borne PU coating technology by creating INSQIN – which adapts the technology to create coated fabrics such as PU leather.
“It’s not just about the technology: we’re addressing the value chain in a different way,” says Nicholas Smith, the company’s global head of textile coating.
A CHANGE OF APPROACH
Bayer MaterialScience has brought the two ends of the chain together, by talking directly to brand owners. “They realised that if they wanted disruptive, game-changing technology they needed to go to the start of the value chain, where the chemistry is created,” he says.
Smith adds that the vast majority of PU leather is made using solvent-borne PU. He says INSQIN uses no solvents, half the energy and 95% less water – as it does not need process water.
PU leather can be used in many applications, including apparel, accessories and furniture, but Smith says footwear is the largest user, accounting for around 70% of the annual 4bn square metres that are produced.
“I hope we’ll see the first INSQIN sport shoes in shops by the end of 2015,” he says.
Smith points out INSQIN can help brand owners boost sustainability in another way – through its Partner Manufacturing Programme. This will build a network of manufacturers of coated fabrics that have been trained and audited in sustainability practices such as restricted substances, chemical inventory lists and chemicals management, storage and handling.
Bayer MaterialScience has teamed up with a testing house, which will audit the manufacturers. This will help the producer to recommend potential manufacturers to brand owners – safe in the knowledge that they are trained in sustainable practices.
“We’re currently working towards having our first INSQIN partner manufacturer by the end of 2014,” he says. “The more partners we have, the better.”
Global News + ICIS Chemical Business (ICB)
See the full picture, with unlimited access to ICIS chemicals news across all markets and regions, plus ICB, the industry-leading magazine for the chemicals industry.
Contact us
Partnering with ICIS unlocks a vision of a future you can trust and achieve. We leverage our unrivalled network of industry experts to deliver a comprehensive market view based on independent and reliable data, insight and analytics.
Contact us to learn how we can support you as you transact today and plan for tomorrow.
READ MORE
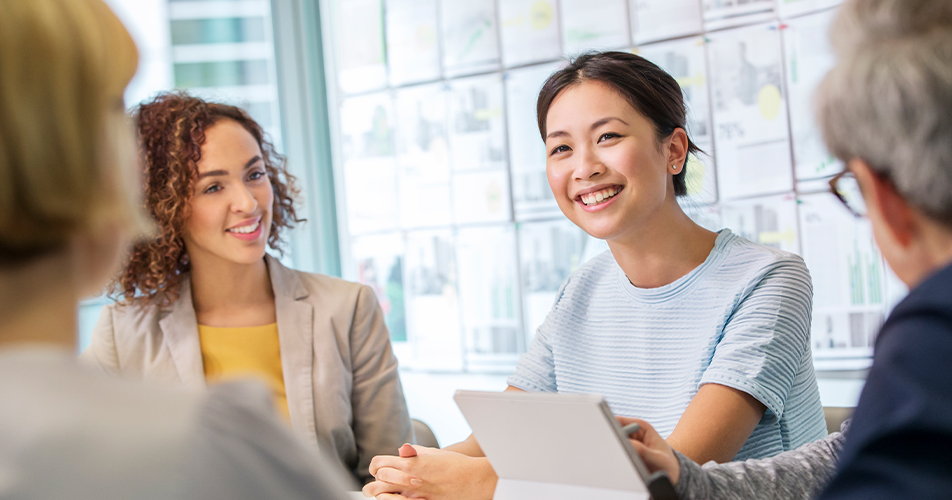