Development of bio-paraxylene and PTA on the rise
Doris De Guzman
12-Mar-2012
The polyester market will soon feature renewable alternatives to petroleum-based paraxylene and purified terephthalic acid, as companies push for more R&D
The quest for 100% plant-based polyethylene terephthalate (PET) might be completed sooner than the 2020 time frame that US beverage companies such as Coca-Cola and PepsiCo initially estimated, since the development of bio-based purified terephthalic acid (PTA) continues to rise.
|
---|
© Coca-ColaThe fruit of Coca-Cola’s Vault of the Secret Formula could soon be bio-bottled |
Coca-Cola’s partnership announcement in December with US renewable chemical firms Gevo, Virent and Dutch firm Avantium set the global PET market abuzz as Coca-Cola assigned the companies to develop alternatives to petrochemical-based PTA for use in its PlantBottle PET beverage packaging.
Coca-Cola’s PlantBottle is currently made from 30% sugarcane-based monoethylene glycol (MEG) and 70% petroleum-based PTA by weight. The production of MEG from plant-based ethanol has long been established, but the path towards bio-based PTA is still under development. PTA is mostly produced by the catalytic liquid phase oxidation of paraxylene (PX) in acetic acid in the presence of air. Nearly all PTA is consumed in polyester production including polyester fiber, PET bottle resin and polyester film.
The global PTA market represents great potential for bio-based alternatives – more than 50m tonnes/year, says Avantium CEO Tom van Aken. “PET bottles are a 15m tonne/year market based on resin volume with a strong pull for green material.”
The global PX market, meanwhile, is estimated at 30m tonnes but demand is expected to double to 60m tonnes by 2020, says Kieran Furlong, director of chemicals at Virent. “If buyers use a rule of thumb of sourcing at least 10% of their needs from alternative sources, that would be a market for bio-PX of 6m tonnes in 2020,” he adds.
“The PX market is large but not too large for renewable alternatives to get into,” says Furlong. Aside from consumer pull towards renewable-based materials, Furlong notes that another future driver for bio-PX demand is the expected structural shift of PX supply as crackers move to lighter feedstocks and less aromatics are produced. This is the result of the shale gas boom in North America. “The economics of running naphtha reformers is also undermined by cheaper natural gas. Current predictions are that PX will be short for some years to come. All in all this is a ‘Goldilocks’ opportunity, where all of the factors seem to be just right for the introduction of bio-PX,” he adds.
RACE TO COMMERCIALIZATION
Virent is looking to produce a sugar-based aromatics stream containing benzene, toluene and xylenes using traditional chemical catalytic processing.
The aromatic stream is further processed to PX, which Virent will commercialize under the trademark BioFormPX.
The company expects to have its first commercial-scale bio-PX plant on line by 2015. “We are in the midst of site selection for this facility right now but have not yet decided on a final location,” says Furlong. “We envision building and operating this plant with a partner and discussions to this end are currently underway.” Virent did not disclose the bio-PX volumes required for Coca-Cola’s supply, citing its confidentiality deal with the beverage company.
Gevo plans to produce bio-based PX by converting fermentation-derived isobutanol to PX using several traditional chemical processes such as dehydration, dimerization, and cyclization. Gevo is currently working on bio-isobutanol-based PX in a contracted facility at Silsbee, Texas, US, owned by US specialty chemical firm South Hampton Resources. Gevo is targeting commercial production of its bio-PX by 2014.
The company is already expecting its first bio-isobutanol plant later this year in Luverne, Minnesota, US, with capacity of 18m gal/year. Its second plant with 38m gal/year capacity is expected to start in 2013 in Redfield, South Dakota, US. Aside from its Coca-Cola partnership, Gevo also has a non-binding supply agreement with Japan-based Toray Industries, which claimed in November last year that it was able to develop the world’s first 100% bio-PET fiber in a laboratory scale using Gevo’s bio-PX.
According to Gevo’s initial public offering (IPO) filing with the US Securities and Exchange Commission in February 2011, Toray is expected to start purchasing 1,000 tonnes/year of bio-PX from Gevo beginning on or after 2012, which would potentially increase to 5,000 tonnes within five years.
Production of 5,000 tonnes/year of PX is expected to require 2.3m gal of isobutanol, according to Gevo. “We believe that the paraxylene can be produced by third-party manufacturers using isobutanol. We intend to solicit commitments from these manufacturers to purchase our isobutanol in order to supply Toray Industries,” Gevo said in the filing.
Avantium, meanwhile, is developing a new sugar-based monomer called furan dicarboxylic acid (FDCA), which can be reacted with MEG to make polyethylene furanoate (PEF), an alternative to PET resin.
|
---|
|
The company claimed its PEF bottle has a better oxygen and carbon dioxide barrier than PET. Avantium said it has already reached the yields and process conditions where it can compete on price with petroleum-based PTA. “Now we will need to reach the scale needed to be cost-competitive. For FDCA to be cost competitive, we need to produce at around 300,000 tonnes/year-scale,” says Van Aken. He adds: “We believe our process has inherent process economic benefits over bio-PTA processes. Using chemical catalytic processes and assets provides the necessary speed and efficiency, retaining all the carbon from the feedstock – thus requiring a smaller amount of carbohydrate feedstock per ton of resin, as well as being an excellent fit with existing PET production installations.” Avantium expects to start commercial production of FDCA and PEF in 2015.
Van Aken says it is working on site selection for its first commercial plant, which the company is prepared to build and operate itself. “Involving a [feedstock or production] partner to accelerate the rollout is an interesting option. Beyond the first plant, we envision that industrial scale production will take place on every continent to serve the needs of our partners,” Van Aken adds. The disadvantages of the bioprocessing routes to PX stem from the fact that they are in the developmental stage and thus are unproven on a fully integrated commercial basis, notes Eric Bober, a member of biotechnologies and renewable markets team at US consulting firm Nexant.
The company has been assessing bio-routes to PX/PTA/PET as well as other bio-based polymers, focusing on technologies, cost of production and comparisons to traditional routes. “Capital expenditures for the initial commercial plants will be high, as these are first-of-a-kind plants as opposed to the ‘nth’ plant status of petrochemical facilities,” says Bober. A world-scale conventional PX plant is now 1m tonnes/year and likely four times as large as a bio-PX line, adds Bober.
Bio-derived products will likely locate near the available renewable feedstocks, which could increase logistics costs relative to the conventional supply chain.
“Consumers of PX, PET and their bio-derived equivalents are largely clustered in the US Gulf Coast. The Great Lakes region might prove to be an efficient location for bio-routes,” says Bober.
MORE GREEN PTA ROUTES
More bio-processing is being developed to produce renewables-based PTA, said Jim Lunt, managing director for US consulting firm Jim Lunt and Associates, speaking at a bioplastic seminar the company held on February 20.
Lunt cited US start-up firm Anellotech’s single-step catalytic fast pyrolysis process to convert biomass to benzene, toluene and xylene; US firms Amyris and Genomatica’s processes that can convert sugar-based muconic acid to PTA; and Saudi Arabia-based SABIC’s patent claiming PX production via use of terpenes such as limonene found in citrus fruits.
US start-up bio-gasoline developer Primus Green Energy notes that its biomass gasification and “syngas-to-green” patented processing can be tuned up to make up to 80% aromatics. It currently produces a 93 octane gasoline, according to George Boyajian, vice presdient of Primus Green Energy.
“We are currently producing xylenes and toluenes in equal proportion but have not fully characterized the isomers that we are producing,” he says. “Chemical companies have approached us about these products given the recent news from Coca-Cola, which suggests that green plastics are here to stay.”
Based on publicly available information, Nexant’s Bober says Anellotech’s process looks to be cost competitive with petroleum-based PX.
Global News + ICIS Chemical Business (ICB)
See the full picture, with unlimited access to ICIS chemicals news across all markets and regions, plus ICB, the industry-leading magazine for the chemicals industry.
Contact us
Partnering with ICIS unlocks a vision of a future you can trust and achieve. We leverage our unrivalled network of industry experts to deliver a comprehensive market view based on independent and reliable data, insight and analytics.
Contact us to learn how we can support you as you transact today and plan for tomorrow.
READ MORE
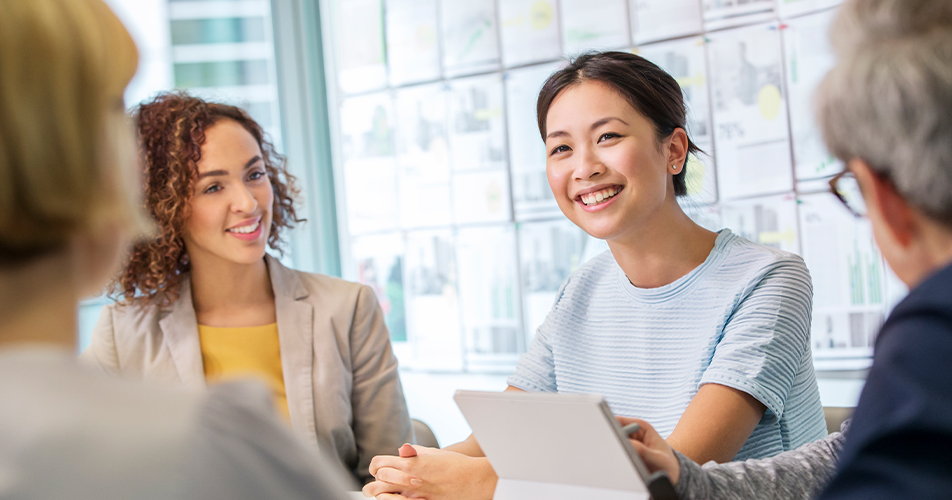