On-purpose technologies ready to fill propylene gap
Clay Boswell
15-Apr-2012
|
---|
© Rex Features |
Propylene was once little more than a disposal problem for cracker operators, but efforts to find uses for it have been so successful that its price exceeds that of its co-product, ethylene, and demand threatens to overtake supply. With traditional sources of propylene increasingly unable to meet market requirements, doors are opening to on-purpose production technologies.
Some of these technologies have been used for many years where local factors support the economics, but naphtha-fed steam crackers and the fluid catalytic cracking (FCC) units of oil refineries continue to dominate production, together supplying 90% of the market. In both cases, propylene is a secondary product, with the result that demand for propylene often has less influence on propylene supply than do developments in the gasoline and ethylene markets, and complications abound.
For example, if gasoline prices are high, oil refiners may increase operating rates. More gasoline means more propylene; but high fuel prices mean refiners may prefer keeping the propylene to make octane-boosting alkylate.
If gasoline demand is low and oil refiners cut operations, propylene and naphtha output will both fall. And since steam crackers need naphtha to make propylene, their own output will decline, compounding the supply problem. Ethylene is less sensitive to developments in the oil refining sector because it can also be made by cracking ethane, a component of natural gas. The amount of propylene obtained by this route is negligible.
North American propylene consumers must contend with a consequence of this relationship. Ethane prices in the region have fallen with the exploitation of shale gas reserves, and the cheap ethylene produced from this ethane has given North American chemical producers a feedstock advantage. The same development has put naphtha-fed steam crackers at a disadvantage, and with many of them shutting down or reconfiguring to handle ethane, the associated propylene production has been lost.
The result is a tight propylene market that is sensitive to supply disruptions. In late 2010, the price of propylene in the US soared after a series of cracker outages, and downstream markets took months to recover.
Conditions such as these hurt the global petrochemicals market, says consultancy Nexant, which recently published a new report, Evolving Propylene Sources – Solution to Supply Shortages?
“Competition between propylene derivatives and similar chemicals will no longer be maintained at current levels, leading to widespread substitution or reduction in propylene derivative growth in response to rapidly rising propylene prices,” the firm warns. The markets for polypropylene and important intermediates such as cumene, acrylonitrile, acrylic acid, isopropanol and propylene oxide are at risk, says Nexant, and they “will eventually experience a reduction in growth, especially if additional supplies of propylene cannot be found.”
ON-PURPOSE PROPYLENE
Multiple “on-purpose” propylene technologies offer a solution, says Jeffrey Plotkin, vice president at Nexant.
One approach is to increase the proportion of propylene generated by FCC units. Although oil refineries supply about 30% of the global propylene market, FCC units have historically been optimized for the production of gasoline, so that propylene typically accounts for a paltry 3-6% of their output.
To address the problem, engineers have modified the zeolite catalysts, hardware, and operating conditions employed by FCC units. Variously called enhanced FCC, deep catalytic cracking or high-severity FCC, the technology can increase propylene yields to 20% or more of output. However, while propylene yield is increased, gasoline production is reduced by 25-35%, Plotkin notes. Engineering firms that are licensing enhanced FCC technologies include Shaw, Honeywell UOP, Lummus Technology, KBR and Axens.
Three other technologies approach the problem more directly by taking pathways outside of the cracker paradigm: propane dehydrogenation, olefin metathesis and methanol-to-propylene.
The most significant of these is propane dehydrogenation (PDH), which already supplies more than 4m tonnes of propylene annually to the global market. The process is straightforward: propane is passed over a heated catalyst that strips away hydrogen, leaving a double bond in its place.
The price spread between propane and propylene determines the profitability of PDH, says Plotkin, with the result that there can be strong seasonal effects. For many years, he notes, two PDH plants in Europe shut down during the cold months when propane prices rose on demand for heating. With propylene as pricey as it is today, however, the spread favors uninterrupted operation.
Indeed, the bullish outlook has spurred a surge of PDH projects. Ten years ago, barely six PDH units were online, but today there are 15, and at least 10 projects are underway.
Two firms dominate – Honeywell UOP and Lummus. US-based UOP licensed its Oleflex technology to the first operational PDH unit. Operated by PTT Chemical, it went online in Thailand in 1990. Since then, UOP has licensed 19 more PDH plants – 10 last year.
Among them is a 750,000 tonne/year unit that Dow is building in Freeport, Texas, US, with start-up planned for 2015. Dow plans a second PDH facility for 2018. The plants, which will consume propane extracted from shale gas, are part of a strategic shift for Dow, which sold its polypropylene business to Braskem last year. However, propylene remains a key feedstock for the company.
“This is yet another step along the line of putting our precious inputs, propylene in this case, into value-add outputs,” CEO Andrew Liveris said when the deal was announced. “We are lowering our [propylene] buy. By the time our second PDH unit comes on line, we will be 100% captive.”
In February, Formosa Plastics announced its own plan to install a 600,000 tonne/year PDH unit at its Point Comfort, Texas, US facility alongside an 800,000 tonne/year olefins cracker and a 300,000 tonne/year polyethylene plant, with start-up expected in 2016.
PDH – AN ATTRACTIVE OPTION
For propylene consumers who do not want co-products, PDH is an attractive option, says Peter Piotrowski, vice president and general manager at UOP. “PDH requires modest capital investment for olefin production and can easily be back-integrated for an existing propylene consumer, lending itself to project viability. Places with propane at low cost, such as the US and the Middle East, or regions looking to lessen propylene imports, like China, [are] candidates for PDH.”
Piotrowski says UOP’s Oleflex technology provides the lowest cost of production and the highest return on investment, owing to low operating and capital costs, high propylene yield and reliability, and maximum operating flexibility.
Lummus, which licensed its first PDH unit in 1992, may see the matter differently. Ten PDH units have licensed Lummus’s Catofin technology, among them PetroLogistics’ 544,000 tonne/year unit in Houston, Texas, which began operating last year.
“The CATOFIN technology has a unique approach for the reactor and catalyst system that provides the highest conversion/selectivity combination,” says Lummus spokeswoman Maria Principe. “The base metal catalyst system also contributes to the low OPEX [operational expenses] while surpassing all HSE [health, safety & environment] requirements.”
German engineering firm Uhde, a newcomer to the field, has licensed its PDH technology to a 350,000 tonne/year unit in Port Said, Egypt, operated by the Egyptian Propylene and Polypropylene Company. Called STAR, short for Steam Active Reforming, the process includes an oxidation step that generates heat, reducing the overall energy requirement.
Olefin metathesis proceeds by a completely different mechanism, and it therefore accommodates different circumstances. The feedstocks are ethylene and butylene. The two are mixed, and a catalyst coaxes each butylene molecule to donate one of its four carbons to a two-carbon ethylene molecule. The result is two three-carbon propylene molecules.
“The key determinant in olefin metathesis is the price difference between ethylene and propylene,” says Plotkin. “That’s why it has caught on only in the past 10-12 years, when propylene prices began to catch up and even surpass ethylene. Historically, propylene prices were always 15% lower than ethylene, so olefin metathesis made no sense except perhaps in special situations.”
A source of butylenes is essential. Typically this would be a naphtha cracker, but butylenes can also be obtained by the dimerization of ethylene.
A Borouge facility in Abu Dhabi is able to take this route owing to the extremely low cost of ethane there.
Lummus rules this segment with its Olefins Conversion Technology (OCT). Discovered by Phillips Petroleum in 1964, it was first commercialized to make propylene in 1986.
“Our OCT process is unique in that the reaction is energy neutral. All other production routes require substantial input of energy to produce propylene,” says Principe. “OCT provides the lowest [capital expense and operating expense] of all the known propylene production processes, with the lowest production of by-products.”
She says that the current wave of OCT projects began in 2000, when the technology was installed as part of the steam cracker project in Sabina, Texas, US, a joint venture between BASF and Atofina (now Total Petrochemicals). Fifteen OCT units are now in the project phase.
“The OCT process is a relatively modest investment to maximize propylene production where crackers and refineries have underutilized butylenes, which typically have a much lower value than propylene,” Principe points out. “These OCT facilities range in size from 60 to 300 KTA.” The dimerization variation can be run at larger scales, she adds.
The third option, methanol-to-propylene (MTP), becomes viable when inexpensive methanol is available. UOP’s Advanced MTO (methanol-to-olefins) process converts methanol to propylene and ethylene in a ratio that can be varied between 1.3 and 1.8 to 1.
UOP has licensed the technology to Wison Nanjing for a unit in China that is scheduled for start-up in mid-2013.
Two other projects were put on hold during 2008 recession, says Piotrowski, but the process has been fully demonstrated at semi-commercial scale by Total Petrochemicals in Feluy, Belgium.
A ROBUST FORECAST FOR MTP
“MTO technology has a favorable outlook for end users who have access to cost-advantaged feedstocks such as natural gas, coal, petcoke and biomass,” says Piotrowski. “The MTO demand forecast is robust and comparable to PDH. We see MTO as an option for areas with inexpensive natural gas – the US, Middle East, and Russia – and large reserves of coal – the US and China.” (See related story on page 32.)
Bio-based processes are at the developmental stage, says Plotkin, but many have been proposed. They generally involve bio-based production of a feedstock such as methanol, ethanol or propanol for conversion to propylene by one of processes described above.
Braskem aims to produce “green” polypropylene. “They take ethylene made from ethanol and dimerize some of it to butylenes,” says Plotkin. “And then they metathesize the butylene with more of the green ethylene. All of these steps use known technology – they don’t have to invent anything. But I think their long-term goal is to develop fermentation technology to take sugar to propanol, and then crack that to propylene.”
Braskem is working with Danish biotech firm Novozymes on the project.
Global News + ICIS Chemical Business (ICB)
See the full picture, with unlimited access to ICIS chemicals news across all markets and regions, plus ICB, the industry-leading magazine for the chemicals industry.
Contact us
Partnering with ICIS unlocks a vision of a future you can trust and achieve. We leverage our unrivalled network of industry experts to deliver a comprehensive market view based on independent and reliable data, insight and analytics.
Contact us to learn how we can support you as you transact today and plan for tomorrow.
READ MORE
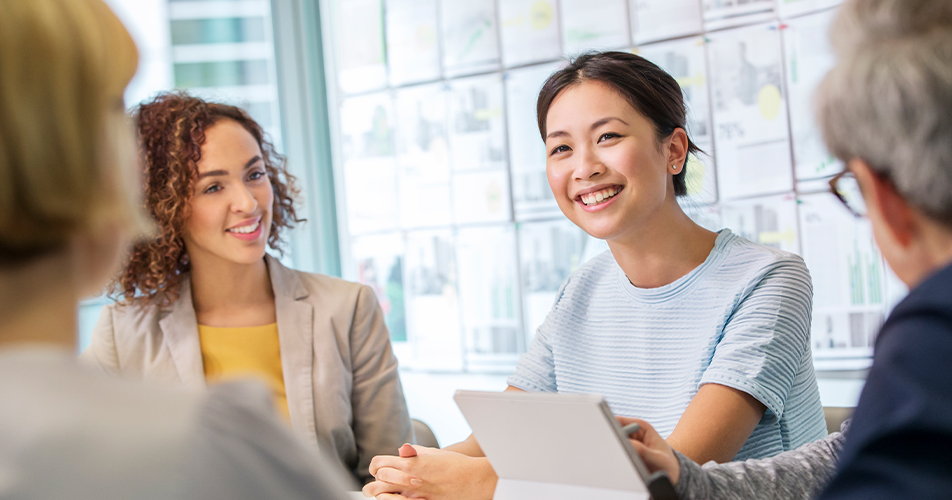