ACC CPI: PU players going green
Doris De Guzman
21-Sep-2012
Companies are looking at opportunities in the growing renewables market, mindful of end users who want green credentials without losing performance
The demand for renewable-based polyurethanes (PUs) continues to rise as manufacturers throughout the value chain within the automotive, footwear, carpet and even furniture sectors seek to differentiate themselves by selling more sustainable products.
Polyurethane is derived from the combination of a polyol and an isocyanate. While isocyanates, so far, have not been made using a bio-based approach, the quest for thermoplastic polyurethane (TPU) manufacturers is to increase their product’s renewable-based content using either polyether polyols or polyester polyols made from plant materials.
|
---|
There is huge potential for growth in the bio-based products sector Copyright: CIAT |
“The biggest demand for bio-based TPUs is from applications that are very close to end users, more specifically OEMs [original equipment manufacturers], in the sports and recreation, automotive and electronics industries,” says Jesus Santamaria, global aliphatic and bio-platform manager at US headquartered speciality chemical firm Lubrizol.
“In these industries, companies are facing high demand for such bio-based materials from customers who want personally to contribute to environment conservancy but without giving away any of the valuable performance that is intrinsic to this engineering polymer,” he adds.
Lubrizol expanded its bio-based TPU portfolio when it acquired Spain’s Merquinsa in December 2011. Merquinsa has been producing plant-derived and reusable TPUs since 2009.
BIO-BASED GROWTH
“Since the launch
four years ago, we have observed a steady growth of BIO TPU
over standard petroleum-based TPU. We are involved in many
ongoing projects pending approval, most of which are new
parts/applications in existing segments that will sustain
tomorrow’s growth,” says Lubrizol’s Santamaria.
US bio-based polyols producer Cargill says it is seeing new uses for renewable-based polyurethanes in seed and fertilizer coating. The company has been producing bio-based polyols in the US and Brazil, with sales around the globe.
“The most use and interest that we see for bio-based PU is in flexible slabstock foam, automotive molded, carpet, and coatings. However, new uses and demand for renewable-based PU are being announced all the time,” says William Gower, technical sales manager, bio-based polyurethanes for Cargill.
BioBased Technologies, another US bio-polyol producer, notes demand growth for renewable-based PU in adhesives and composites markets aside from applications in furniture, slabstock and agriculture.
Construction and automotive industries have been the leaders in adopting bio-based polyurethanes, says Amy Sorrell, CEO of BioBased Technologies. Bio-PUs have reportedly been successful in spray foam insulations and sealants, moulded foams and other automotive parts, carpet backing and padding markets.
“The good news is that bio-based products are still a relatively small segment of the market, so there is plenty of opportunity for growth. Our technical team is working now with companies in these areas that are actively seeking to integrate our bio-based chemicals into their products and processes,” Sorrell says.
In the US, most of the bio-based polyols being marketed use soybean oil for feedstock. US consulting firm Omni Tech estimated the North American petrochemical-based polyols market at 2.6bn lb (1.2m tonnes) as of 2009. Potential substitution by soybean oil-based polyols was forecast at 620m lb (280,000 tonnes) by 2014, especially coming from segments such as construction, transportation, carpet, furniture/bedding, coatings, adhesives, sealants and binders.
US companies active in the development of soybean oil-based PUs include Cargill, BioBased Technologies, Urethane Soy Systems and Dow Chemical.
DRIVING FORCE
According to car
manufacturer Ford Motors,
all of its vehicles built in North America now use soy
oil-based foams in the seat cushions, backs and head
restraints. Ford first used soy oil-derived seating foam in
its 2008 Mustang, in collaboration with automotive management
systems supplier Lear Corporation.
With the soy oil-based foams, Ford said it has helped reduce its annual petroleum oil usage by more than 3m lb.
According to industry analysts, soybean oil-based polyols can offer between 40% and 100% bio-based content, resulting in soy oil-based PU that can have bio-based content between 5% and 60% for flexible and rigid foams.
Cargill says its soybean oil-based polyols under the brand BiOH can allow its customers to create products with typical levels of renewable content from 5% to 20%.
“The greatest challenge from a technical standpoint is maintaining a high renewable content in the polyol and PU without compromising properties,” says Cargill’s Gower. “You have to do this while always keeping end-cost in mind.”
One of the most heard negative comments, according to Cargill, is that the renewable PU technology for PU is not a 100% replacement for petroleum-based products. “However, we are constantly striving to push the limits of renewable content in PU. We are working on the commercialisation of a greater than 50% renewable memory foam product in terms of foam weight,” he adds.
Bayer MaterialScience has already commercialised a range of polyol products for use in PU with renewable content of up to 95% based on natural oils over the past several years, says Paul Nowatzki, innovation manager at the US subsidiary of the German company.
Most of the demand is coming from footwear and apparel applications but Nowatzki says they have seen increasing interest from automotive, construction and consumer electronics customers.
Vegetable oil-based polyols can be derived from soybean, castor, sunflower or rapeseed oil. With castor oil, the polyol can have a bio-based content of 30-100%, allowing for the PU to have a bio-based content between 22% and 70%, according to industry analysts.
Last year, German chemical firm BASF teamed up with Ford to develop the automotive industry’s first castor oil-based foam for the 2012 Ford Focus instrument panel. The PU foam is said to contain more than 10% bio-based content. Over time, Ford says it plans to incorporate castor oil-based foam solutions across more products in its global portfolio.
BASF Polyurethane Systems has been producing bio-based PUs for about a year now and bio-based TPU elastomers for six months, says Brad Martin, new business development and sales manager for BASF’s Elastollan TPU.
Martin says its Elastollan N TPUs have bio-based content ranging between 40% and 4% depending on the grade. The product is commercially available in Asia and Europe but it is expected to be sold in North America soon.
TPUs account for less than 5% of the total production of polyurethane products but represent one of the fastest-growing parts of the industry, according to IAL Consultants in its June 2011 global TPU market report. Footwear and engineering plastics account for more than half of global TPU consumption as of 2010.
“Footwear producers want to market to green-savvy consumers, who want to feel good about the shoes they buy. One way to feel good is to be part of a sustainability message, and a bio-sourced material is one way to help footwear producers offer this to consumers,” says BASF’s Martin.
The company is evaluating more bio-based materials and products every day, he says. “Some of these materials are in production, and we expect to see more in the future,” adds Martin.
BIO-MONOMERS POTENTIAL
Nowatzki says
Bayer MaterialScience now has a much bigger opportunity for
polyurethanes from drop-in bio-based monomers such as those
used to make bio-based polyester polyols. “Our biggest focus
is on drop-in bio-based chemicals to directly replace the
petro-based materials we use today. We are looking at near
drop-ins such as bio-based succinic acid to substitute for
petro-based adipic acid, which may lead to new material
properties,” adds Nowatzki.
The three general types of polyester polyols are traditionally manufactured from aliphatic diacids, aromatic diacids or caprolactone. Renewable chemical companies offering bio-based succinic acid as substitute for polyurethane polyols feedstock include US-based BioAmber and Myriant, BASF and its joint venture partner Purac, based in the Netherlands; and Reverdia, the Netherlands-based joint venture between Dutch firm DSM and France-based Roquette.
For bio-based adipic acid, firms involved in development include US-based Rennovia, Verdezyne, Genomatica, Amyris as well as DSM. BioAmber and Myriant have also noted their interests in developing bio-based adipic acid.
US renewable chemical firm Elevance, meanwhile, has partnered with US polyol producer Stepan to develop and produce vegetable oil-based C18 diacids for polyurethane polyols feedstock.
For polyether polyols, sucrose and sorbitol can be used for rigid foams although bio-based content is typically low at less than 30%, according industry analysts. This results in rigid foam polyurethanes having less than 8% bio-based content.
Other examples of bio-based polyether polyol derivatives include polytrimethylene ether glycol from sugar-based 1,3-propanediol (1,3-PDO) and 1,2-propanediol made from bio-based glycerine.
Bayer MaterialScience, meanwhile is looking to convert carbon dioxide to produce polyether polycarbonate polyols for use in flexible foam. The polyols are being produced in a pilot plant at Bayer MaterialScience’s site in Chempark Leverkusen, Germany.
“The first products based on CO2 are scheduled for market launch in 2015. We are ultimately looking for opportunities that have a positive overall environmental impact and are economically sustainable as well,” says Nowatzki.
With the case of most bio-based drop-in chemicals, most companies involved in this development note that many of their customers are not willing to pay more for these materials.
“Bio-based monomers suppliers are confident in their ability to match or beat petroleum-based prices long-term but in the short-term there are often increased costs,” adds Nowatzki.
The bottom line, according to BioBased Technologies’ Sorrell is that renewable-based PU products need to succeed on three levels to be successfully integrated: price, performance and sustainability.
For more information about bio-based PUs, visit the green chemicals blog
Global News + ICIS Chemical Business (ICB)
See the full picture, with unlimited access to ICIS chemicals news across all markets and regions, plus ICB, the industry-leading magazine for the chemicals industry.
Contact us
Partnering with ICIS unlocks a vision of a future you can trust and achieve. We leverage our unrivalled network of industry experts to deliver a comprehensive market view based on independent and reliable data, insight and analytics.
Contact us to learn how we can support you as you transact today and plan for tomorrow.
READ MORE
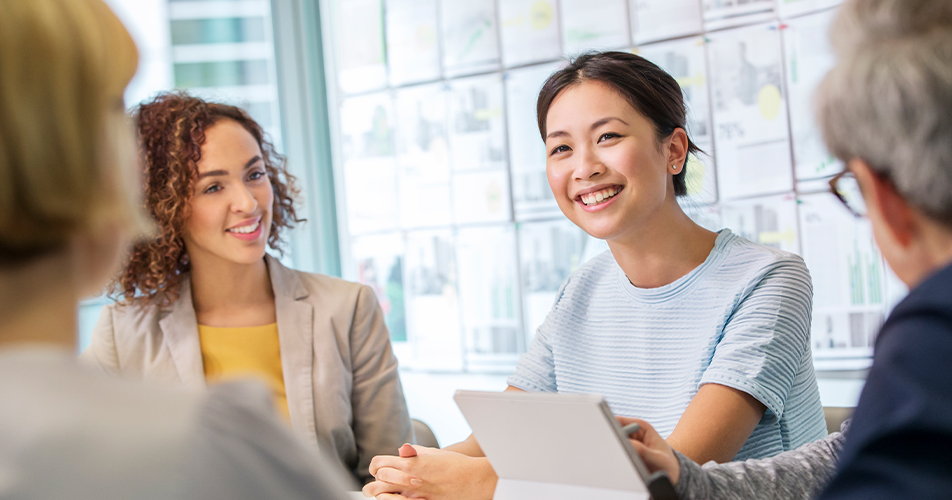