Special report: SABIC takes first steps into renewable polyolefins
Will Beacham
22-Jun-2014
Saudi Arabia’s SABIC plans to manufacture and market a full range of renewable polyethylene (PE) and polypropylene (PP) by feeding “second generation” waste animal and vegetable oil feedstocks into its crackers in Europe.
The project aims to help customers, especially in the packaging sector, meet consumer demand for sustainable, renewable products.
It uses certification from the International Sustainability and Carbon Certification plus (ISCC+) scheme which certifies renewable content and standards throughout the value chain from source to end product.
|
---|
Rex Features SABIC is pushing the green agenda with bioplastics |
SABIC expects its customers also to use the ISCC+ system to show customers the product is from a renewable feedstock.
SABIC has not needed to invest any money in new technology because, say executives, the company’s crackers in Europe are flexible enough to crack animal and vegetable oils without modification. A spokesperson told ICIS the oils and fats are hydrogenated by its ISCC+-certified feedstock supplier.
The company’s Geleen, Netherlands, cracker will be the first to produce the renewable polymers.
The ISCC+ certification works on a “mass balance system” which means that for each tonne of renewable feedstock fed into the cracker, a proportion of the output can be claimed as renewable. SABIC says independent, third party auditors have checked its reliability.
Mark Vester, business unit director for linear low and low density PE in Europe, says: “We source fuels from the market which are renewable, and this is being overseen as a chain of custody by the ISCC+ scheme which gives us the confidence that these sources are renewable. If you bought a certified renewable tonne of PP there is a direct connection between your purchase and our purchase of the certified feedstock.”
He says SABIC is in an advantageous position because it can use the same assets where it processes standard feedstocks. “Our crackers have the ability to crack heavy renewable feedstocks and [hold] a unique position in that respect. We are especially happy that we have found a way to bring renewable poly-olefins to the market in this way. We are now able to offer something to the market that neither SABIC nor others could offer.”
The feedstock comes in a liquid form and its properties are similar to traditional feedstocks.
“At our Geleen site (Olefins 3 and 4) we have differentiated ourselves through the use of various liquid feedstocks… We do not stop and start the cracker for the processing of these [renewable] fuels,” says Vester.
Any form of waste fat or oil which can be converted into a fuel is a suitable feedstock including vegetable oil or animal fat waste from meat processing or waste oils from other industries. The fuels being targeted are termed “second generation” because they do not compete with food.
Vester adds: “Compared to total polyolefin consumption the feedstock is limited. But we believe there is enough second generation to replace the current first generation feedstock which is on the market.”
He described this initiative as a “drop in” solution where the properties of the products produced are identical to SABIC’s current offering. “This means they can be adopted across the value chain without any consequences for further processing or recycling.”
GROWING MARKET
SABIC is now working with its customers to bring these renewables to market as finished goods such as renewable-based packaging.
“The market for renewable polyolefins is limited but we see them growing substantially faster. One of the drivers for the market will be the availability of renewable polyolefins. We are bringing renewable PP to the market which is not yet available. This availability will help to create demand: the polymers will now be available as renewables under the ISCC+ scheme.”
Vester added that the company plans to expand renewable polyolefin manufacturing to its Gelsenkirchen, Germany, site over the next few months.
Very early in the process SABIC consulted with its customers and found that a substantial group had an interest in this solution. It then co-developed some of these products with customers and some of them are now working on certification of their own processes. In principle the whole value chain uses the certification scheme from source to end product. This gives the end product its claim for sustainability.
CUSTOMERS ARE NEARLY READY
“Our work with customers is quite advanced but you need to go from having a [certified] feedstock down the value chain. We expect customers to be ready in the near future. It is available right now and we expect our customers to take it to the market in the form of products or packaging,” says Vester.
He declines to say if the waste oils and fats feedstock has yet been trialled in the crackers. He also does not comment on feedstock or product pricing, saying that SABIC deals with this with customers, confidentially.
|
---|
SABIC’s Geleen cracker is flexible |
“We’re always talking about small steps which contribute to sustainability. Resource-efficiency is high on our agenda and this comes from a totally different angle. It’s complementary and adds to the range of solutions SABIC has to offer to the marketplace.” He believes the project fits in perfectly with the company’s leadership in sustainability agenda.
According to Steven de Boer, SABIC’s director, innovation and sustainability for the polymers business unit, for SABIC, as a targeted action, this initiative is new.
He adds: “We have set ourselves the objective to do our homework as well as possible so that all our internal actions are as resource-efficient as possible. We also have the support of the value chain. It’s part of our strategy and there are more examples coming in the pipeline.”
SABIC claims this is the first time the market in Europe has been offered second generation polyolefins of this type, and the first time that renewable PP has been available to this market.
In October 2013, BASF unveiled a similar method of certifying products as renewable through the mass balance system. It uses third party verifier TUV SUD and has certified superabsorbants, performance polymers and other intermediates.
BIO-NAPHTHA COMES OF AGE
Biofuel production produces streams of waste material which are not suitable for biodiesel or other biofuels.
In 2012 Finland’s Neste Oil launched a bio-naphtha product under the brand NExBTL. It uses hydrogenation of natural oils to produce bio-diesel, jet fuel and propane as well as naphtha. Bio-naphtha can be fed into many crackers without the need to modify the plant.
In April 2014, UK-based Solena fuels launched a project with British Airways to convert landfill waste into jet fuel with bio-naphtha as a by-product.
According to a report by consultant Nexant, bio-naphtha technology is also being developed using natural oils by France’s Total, the US Energy & Environmental Research Center – a collaboration between the University of North Dakota and US refiner Tesoro – and US gas-to-liquids group, Syntroleum.
Biomass routes to bio-naphtha are being developed by US fuels groups Rentech and Solena as well as Finland’s UPM. Sasol and Shell both have bio-methane routes to bio-naphtha.
Neste Oil claims it is one of the world’s first companies to supply bio-naphtha on a commercial scale. Its NExBTL naphtha is produced as part of the NExBTL renewable diesel refining process at sites in Finland, the Netherlands and Singapore.
Bioplastics produced from NExBTL naphtha can be used in numerous industries that prioritise the use of renewable and sustainable raw materials, such as companies producing plastic parts for the auto- motive industry and packaging for consumer products.
According to Neste Oil, the mechanical and physical properties of bioplastics produced from NExBTL renewable naphtha are fully comparable with those of plastics produced from fossil naphtha; whilst the carbon footprint of these plastics is smaller than that of conventional fossil-based plastics.
It says bioplastics produced from NExBTL bio-naphtha can be recycled with conventional fossil-based plastic products, and used as a fuel in energy generation following recycling.
Global News + ICIS Chemical Business (ICB)
See the full picture, with unlimited access to ICIS chemicals news across all markets and regions, plus ICB, the industry-leading magazine for the chemicals industry.
Contact us
Partnering with ICIS unlocks a vision of a future you can trust and achieve. We leverage our unrivalled network of industry experts to deliver a comprehensive market view based on independent and reliable data, insight and analytics.
Contact us to learn how we can support you as you transact today and plan for tomorrow.
READ MORE
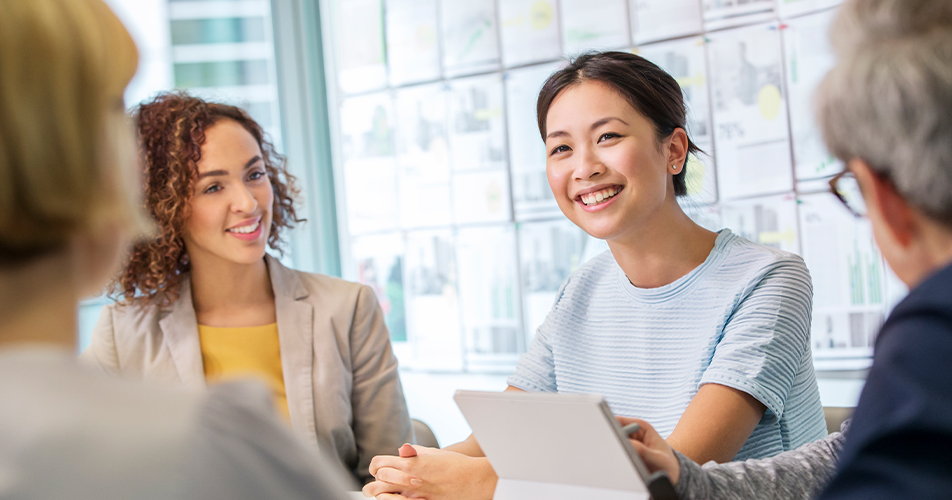