ACC: Product stewardship – Taking greater responsibility
Cynthia Challener
19-Sep-2014
Across the polyurethane (PU) value chain, there is a strong emphasis placed on the proper handling of isocyanates (including di-isocyanates and polyisocyanates), which are key building blocks for PU products.
At the company and industry-wide level, there is recognition that appropriate training and education can raise both the awareness and safety of employees and contractors working with isocyanates.
Extensive product stewardship efforts by isocyanate manufacturers and industry trade groups, often conducted in close cooperation with federal and state regulatory agencies, have resulted in a dramatic improvement in the safety performance of the industry.
|
---|
Rex Features |
As the benefits of these efforts become increasingly apparent, the Center for the Polyurethanes Industry (CPI) of the American Chemistry Council (ACC) continues to work with other key trade associations to support the needs of the PU industry as it grapples with ongoing challenges, such as the National Emphasis Program (NEP) on isocyanates being implemented by the Occupational Safety and Health Administration (OSHA) and the potential regulation of spray polyurethane foam (SPF) insulation and roofing by California’s Department of Toxic Substances Control (DTSC).
Manufacturers of isocyanates take product stewardship very seriously. Huntsman uses a holistic approach to ensure that its own employees and its customers and their employees have the necessary education, training and equipment to safely work with isocyanates. Cynthia Graham, a senior toxicologist with Huntsman, says it is important that anyone handling isocyanates understands the hazards and how to minimise exposure.
CUSTOMER ASSESSMENTS
To that end, each new customer of Huntsman is subjected to an assessment by the company, the goal of which is to evaluate the process in which PU products are used/handled to identify exposure potentials, handling issues and control measures that are in place or needed before product is shipped. Huntsman, along with other CPI member companies, also provides extensive customer training on the safe handling of isocyanates.
Numerous types of materials are also offered by member companies and the CPI, including video and audio files and written brochures. Such an approach is common throughout the industry, according to Graham.
At the industry level, the CPI has a product stewardship committee with representatives from both isocyanate manufacturers and PU end-users. “This CPI committee is a great voice of, and resource for, the industry,” says Brenda Pollack, principal regulatory specialist for packaging solutions provider Sealed Air and chair of the committee.
“In order for the polyurethane industry to grow, we need to ensure that safe systems are in place and that the industry as a whole is on the same page. From the perspective of an end-user, I believe that the work of the CPI product stewardship committee has led to enhanced safety at all levels, and as a result, the entire industry has benefited,” she says.
Pollack points specifically to the training resources that have been developed and made available online as having a significant impact on the industry. “These resources are readily accessible and address the most common questions that users of isocyanates are apt to have.
For small businesses that don’t have a lot of resources, access to this type of online training is very valuable,” she adds. Statistics on the use of online resources and the completion of online training courses also provide a good indication of how the industry is doing, according to Pollack.
OUTREACH
PROGRAMME The Center for the Polyurethanes Industry (CPI) is closely following the US Occupational Safety and Health Administration (OSHA) on the agency’s National Emphasis Program (NEP), a three-year initiative developed to focus OSHA resources on occupational exposure to isocyanates. The enforcement and outreach programme is intended to raise the awareness of employers, workers, and safety and health professionals about the potential health effects associated with occupational exposure to isocyanates. OSHA is targeting facilities in multiple industries that involve exposure to isocyanates. Even sites with fewer than 10 workers are covered, as are relevant federal agencies that handle isocyanates, and OSHA will be evaluating all activities that are covered by safety standards, from hazard communication to record keeping to operating processes and procedures. The OSHA NEP initiative relates to the industry’s product stewardship efforts because it is focused on the safe use of isocyanates. “We are eager to learn what areas, if any, OSHA identifies as needing improvement so that we can provide guidance to the industry,” says Lee Salamone, senior director of the CPI. William Robert, polyurethanes product steward at BASF and a member of the CPI product stewardship committee, also notes that regardless of the results of the NEP, the CPI and individual companies such as BASF will continue to develop additional data on isocyanates with the goal of further enhancing the safety of the polyurethanes (PU) industry. While the OSHA NEP is under way, companies in the PU industry (and all industries, in fact) are also working towards the 1 June 2015 deadline for hazard reclassification and the production of new labels and safety data sheets that are in compliance with OSHA’s new Hazard Communication Standard (HCS) promulgated in 2012, which is aligned with the Globally Harmonized System (GHS) for chemical classification and labelling. Companies should have already completed employee training – the deadline was December 2013. “This new regulation involves the biggest change to the HCS that we have seen in many years and involves a new approach to communicating hazards associated with the use of chemicals in the workplace,” observes Brenda Pollack, principal regulatory specialist for PU foam manufacturer Sealed Air and chair of the committee. Implementation will take significant time and resources as a result. |
Online training courses are available on the CPI website for both low-pressure and high-pressure SPF. Guidance documents on the handling, transportation and storage of isocyanates are also available. CPI tracks the website statistics for these resources and has a good indication of their level of use.
“We are very excited to see a significant increase in the number of completions for the training programme for high-pressure application, which has reached the 10,000 mark,” notes Heather Palfrey, environmental health and safety manager at the CPI. She attributes this success to the robustness of the training programme and the fact that the Spray Polyurethane Foam Alliance (SPFA) now requires completion of the CPI online course as part of its certification process. Many isocyanate manufacturers also require their customers to complete the online training programme.
The industry should be very proud of both the CPI training programme and the certification programme adopted by the SPFA, according to Peter Davis, chairman and CEO of foam manufacturer Gaco Western. “The SPFA programme was developed by contractors for contractors and is designed to meet all of the requirements for compliance with all standards that are relevant to spray foams. It is a very extensive programme and tremendously valuable. In addition, it really is a unique and extraordinary accomplishment that is a very promising development for the industry,” he says.
“CPI has always been very good at making information accessible to the people in the industry that need to have it. Most importantly, the information the organisation provides is the best scientific information available,” says William Robert, polyurethanes product steward at BASF and a member of the CPI product stewardship committee. Most recently, much of the important safety and handling information has been translated into Spanish and other languages to make it easier for non-native English speakers to fully understand these important issues, he notes.
All of these efforts have led to real progress over the past 10 years, according to Robert. “The industry is now working from the same page. In addition, we have covered a lot of ground with respect to the safe handling of isocyanates and increased our understanding of the chemistry and properties of this class of compounds.
“As a result, we know a great deal more than we did before, including both positive and negative aspects. That knowledge has enabled us as isocyanate manufacturers to develop products that are safer and have reduced health and environmental profiles,” he observes.
DECLINING ASTHMA RATES
Although there is no way to directly tie the product stewardship efforts of the industry to recent declines in the rates of occupational asthma (OA) due to isocyanates, Lee Salamone, senior director of the CPI, believes that there is a connection with the increased training and education that workers across the value chain are now receiving with respect to the safe handling of these materials.
“Although data does not support the claim that di-isocyanates are the leading cause of occupational asthma; this statement is often made in the literature,” says Huntsman’s Graham. In response, she and colleagues at the International Isocyanate Institute conducted an extensive review of OA data, including national and state/province-based registries, surveillance schemes and compensation statistics with various metrics for rates of di-isocyanate-related OA and investigated the trends.
First, they found that surveillance data from the Centers for Disease Control and Prevention (CDC) indicates that all isocyanates together account for only 5% of the top 10 leading causes of occupational asthma, and therefore isocyanates are not the leading cause of OA. “Furthermore, methylene di-isocyanate (MDI), the main di-isocyanate used for the production of SPF, is only one of the isocyanates grouped into this category, which makes the number of MDI work-related asthma cases even lower,” Graham notes.
This national result is also supported by California data. California is one of several states to receive funding from the National Institute for Occupational Safety and Health (NIOSH) to conduct surveillance of work-related asthma. The California Department of Public Health (CDPH) Services’ Sentinel Event Notification System for Occupational Risks (SENSOR) programme was developed to identify primary and secondary cases of work-related asthma.
In the agency’s most recent report from May 2013, it is stated that during 1993-2008, isocyanates did not make the top 17 list of agents causing work-related asthma. Furthermore, in a May 2014 personal communication from Jason Wilken of the CDPH, a total of just 10 cases of asthma related to MDI were reported from 1993-2014 in California. Furthermore, in Michigan, work-related asthma cases attributed to di-isocyanates have fallen from 22.9 cases/year in 1988-1997 to 6.4 cases/year in 2005-2010, according to a report generated as part of the state’s SENSOR project.
It is also important to note, according to Graham, that the reduction in OA cases due to isocyanates is not occurring just in the US. In the Canadian province of Ontario, the annual rate of successful isocyanate-related worker compensation claims fell from an average of 30.5/year during 1980-1993 to 7.4/year from 1998-2002. Similarly, while 22% of OA cases in the UK were attributed to isocyanates from 1989-1991, that number declined to 14% for the period 1992-2001. In France, the percentage of OA cases attributed to isocyanates declined from 12.7% to 6.2% from 2001-2009, a statistically significant decline even while the total number of OA cases due to all agents fell.
|
---|
Rex Features Levels of occupational asthma have been falling |
“These results for di-isocyanate-related asthma rates clearly show a significant reduction in reported cases,” Graham states. She notes that there is variability from location to location, but such variation is expected given that the method of diagnosis varies widely (simple physician diagnosis as work-related versus specific challenge testing, for example).
“We strongly believe that the benefits of the product stewardship activities of the industry are being realised in these lower OA rates attributed to isocyanates,” Graham asserts. “Toxicity is directly related to the dose, and any substance can be safe or harmful depending on how it is used. Exposure control, training, the proper equipment, and medical surveillance are critical, and product stewardship efforts across the value chain over the last 10 years or so have improved the safety performance of the polyurethane industry with respect to all of these factors,” she adds.
As a consequence of the activities within companies and of the CPI product stewardship committee and other trade associations, the environmental sustainability and safety performance of the PU industry have been noticeably enhanced.
CLOSE COLLABORATION
While working to develop the various training and guidance materials that the CPI now offers, the association has made a point of establishing a collaborative relationship with relevant national and state regulatory agencies. “The industry has made a real effort to provide sound, pertinent scientific data in response to requests from regulatory bodies, because we have a common goal of ensuring that the industry operates in the safest manner possible,” says BASF’s Robert.
The CPI’s Salamone adds: “CPI has a really strong relationship with the federal agencies; we want as many people as possible to have as much accurate information as possible on isocyanates and how to work with them safely.” These relationships are key as the various groups work together to develop indoor air emission standards for spray foam.
Internationally, Salamone notes that the CPI has also developed cooperative relationships with associations from around the world.
MEETING OBJECTIVES
When it comes to regulatory issues, the CPI is ideally positioned to support the PU industry because it partners with companies across the value chain, from raw material and additive suppliers to PU manufacturers. “Consequently, CPI is also a good resource for regulatory agencies, because they can be sure that everyone in the industry is working from the same page,” states Salamone.
The CPI’s Polyurethanes Technical Conference also provides the ideal venue for regulators to meet and discuss key topics with the industry, because they can speak to technical representatives from all parts of the industry and get clarification on any questions they might have about polyurethanes and isocyanates. “One of the missions of CPI is regulatory advocacy, and the conference also provides a great opportunity for attendees to discuss key topics directly with regulators,” Salamone adds.
In addition to the regulatory roundtable, speakers from OSHA, the Environmental Protection Agency (EPA) and California’s DTSC will talk about current regulatory programmes of interest to the industry. A representative from OSHA will discuss the NEP enforcement programme and the results that have been obtained after completion of the first year of the programme, including the identification of any areas for improvement.
A speaker from EPA will discuss proposed regulation on polyurethane foam expansion (blowing) agents that has been created in response to the President’s Climate Action Plan. Finally, a regulator from California’s DTSC will speak about the agency’s inclusion of SPF on the proposed Priority List of products to be regulated under the state’s Safer Consumer Products Act (SCPA).
“Having these speakers at the conference provides the opportunity for face-to-face discussions through which the industry can learn what the agencies are looking for and how industry can address any concerns. Such discussions are invaluable,” points out Salamone.
CONSUMER
PROTECTION
CALIFORNIA’S
SURPRISE MOVE ON SPRAY FOAM
Another challenge for the spray polyurethane foam (SPF) industry was raised in March 2014 when the California Department of Toxic Substances Control (DTSC) issued its proposal to require an Alternatives Assessment and possible follow-on regulation of SPF for home and building insulation, weatherising and sealing, and roofing applications under the state’s Safer Consumer Products Act (SCPA). This caught the industry by surprise, as the agency made no indications in any prior discussions with industry trade groups or manufacturers and users in California that it intended to evaluate SPF.
Listing a product on the initial Priority Products list imposes no new regulatory requirements on manufacturers and is only the second step of a four-step process that could eventually lead to DTSC implementing a regulatory response.
“This decision was completely unexpected, because the SCPA is designed to protect consumers from hazardous chemicals in consumer products, and spray foam is not a consumer product, but a commercial product used by certified, professional applicators,” says Peter Davis, chairman and CEO of foam manufacturer Gaco Western.
The American Chemistry Council (ACC)/Center for the Polyurethanes Industry (CPI) and the Spray Polyurethane Foam Alliance (SPFA) are frustrated by the DTSC decision to list SPF. They have worked closely with the US Environmental Protection Agency (EPA), the US Occupational Safety and Health Administration (OSHA), and other federal agencies on health and safety initiatives, and real progress has been made in implementing training and certification programmes to ensure the safe manufacture and application of SPF. Both groups have also worked with various California regulators on the SCPA and other issues, such as flame retardants and energy efficiency.
“What is perhaps most confusing is the assumption that because isocyanates are on the list, spray foam should be there as well,” Davis observes. EPA has stated in its chemical action plan that cured isocyanates, that are in installed SPF, are considered to be inert and non-toxic.
Davis goes on to note that DTSC also based its decision on inaccurate information and has posted inaccuracies on its website as well. For instance, DTSC refers to isocyanates that are not actually used to produce SPF and mentions asthma rates among workers in the polyurethanes industry and comments on suspected medical consequences of exposure that have no factual basis.
“Having this erroneous information about SPF on the DTSC website is very damaging to the small businesses in California that provide SPF for home and commercial building owners that are looking to improve the energy-efficiency of their structures,” comments Davis.
In fact, he says many small firms are already losing business because customers are now afraid to use SPF, or won’t use it until the regulatory issue is favourably resolved. At the same time, he notes that it will be very difficult for many buildings in California to meet the new energy-efficiency requirements in the latest building codes without SPF, because it provides a true air barrier and continuous insulation, which cannot be achieved with most other types of insulation.
Identified Priority Products must undergo alternative assessments to determine if “safer” alternatives are available, the results of which will determine any actions to be taken (labelling requirements, use restrictions, bans, etc).
SPF is on the initial draft Priority List for the SCPA. CPI and SPFA are advocating that SPF be delisted. To achieve that goal, a strong grassroots movement has taken form.
“A coalition comprised of spray foam manufacturers and installers, home builders, energy efficiency advocates, and others is working very hard behind the scenes, writing to legislators to make sure they are correctly informed about the issue and that DTSC has based its decision on erroneous information,” Davis explains. ACC, SPFA and isocyanate manufacturers all also continue to try to educate DTSC regulators and participate in the regulatory process.
Global News + ICIS Chemical Business (ICB)
See the full picture, with unlimited access to ICIS chemicals news across all markets and regions, plus ICB, the industry-leading magazine for the chemicals industry.
Contact us
Partnering with ICIS unlocks a vision of a future you can trust and achieve. We leverage our unrivalled network of industry experts to deliver a comprehensive market view based on independent and reliable data, insight and analytics.
Contact us to learn how we can support you as you transact today and plan for tomorrow.
READ MORE
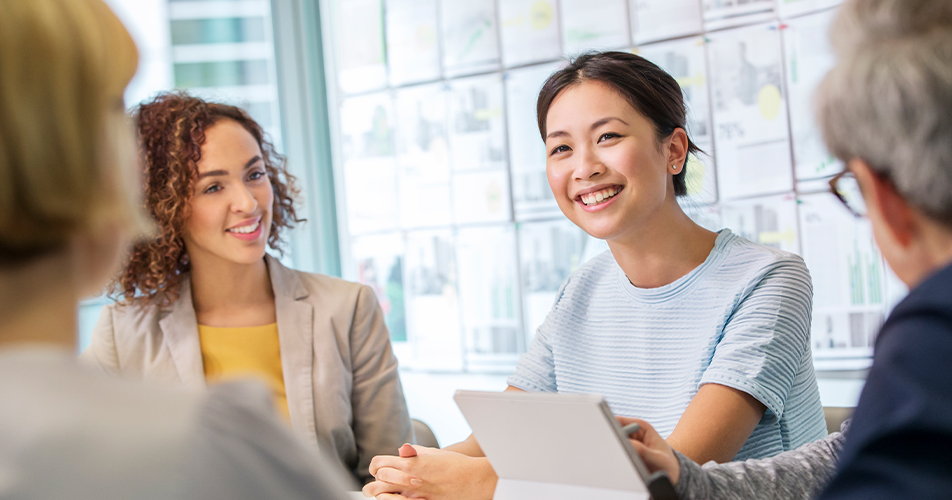