ICIS Innovation Awards: Revolution in the air
John Baker
17-Oct-2014
Big data, cloud computing, advanced manufacturing and internet connectivity promise a new industrial revolution, but much innovation is needed to realise the vision
Are we on the brink of a fourth industrial revolution? Many in industry, information technology (IT) and management consulting believe we are and that higher manufacturing efficiencies in more flexible factories could be achieved over the next 10 to 20 years.
|
---|
Revolution in the air Copyright: Rex Features |
The concept of Industry 4.0, as it has been dubbed, seems first to have emerged in Germany a few years ago, when leading companies such as Robert Bosch and Siemens began to look into the potential from combining physical manufacturing systems with the benefits of big data and cloud computing, to create a cyber-physical system.
In the US, GE has been a prime mover in this area with its The Industrial Internet initiative. It believes this is capable of bringing about a profound transformation to global industry by connecting more intelligent machines, advanced analytics and people at work.
“This deeper meshing of the digital world with the world of machines has the potential to bring enormous economic benefits… boosting global GDP by as much as $10-15 trillion over the next 20 years through accelerated productivity growth,” says GE. The US has also established a Smart Manufacturing Leadership Coalition to facilitate adoption of intelligent manufacturing.
Such cyber-physical systems (CPS) might well form the basis for the next industrial revolution, says Neil Checker, a partner at Roland Berger Strategy Consulting, based in Germany. Industry 4.0 has the potential to transform manufacturing and economies, he explains, enabling the introduction of new products and new ways of making existing ones.
The development, he adds, also has the potential to be truly disruptive, breaking down the competitive status quo between both countries and enterprises. It will bring in new requirements for the workforce and supply chain infrastructure.
“The coming together of IT and manufacturing has the potential to create an integrated information flow from customer back to raw materials input,” he maintains. Customer and market feedback and intelligence managed by big data will open up new possibilties.
“While this is more relevant to the B2C sector right now, the technology lends itself to use in those sectors of the chemical industry that have fragmented and diverse customer needs.”
But why Industry 4.0, and why the fourth industrial revolution? Commentators point to three earlier steps along the path to manufacturing automation: the first industrial revolution was based on machinery and power to mechanise previously manual tasks, such as weaving; the second occurred when mass production on an assembly line was introduced, notably in the car industry; and the third involved the use of programmable logic controllers (PLCs) and robots to automate many remaining manual tasks.
Industry 4.0 will take this automation further, linking automated factories with one another, and with huge amounts of computer-held information gathered from multiple sources and held in networked IT systems or the Cloud. Manufacturing, it is argued, will become more efficient, more responsive and more flexible, opening up changes with respect to products and services, processes and business models and competitive behaviour.
“It is early days yet and as a consultancy we are still working through the implications for various industry sectors,” says Checker, whose expertise lies in the chemical industry.
But he is certain it will create a lot of interest as companies are seeking to drive profitable growth and gain competitive advantage, especially as global economies shift gear to lower overall growth levels.
Embracing Industry 4.0 will be vital for European industry in particular, says Checker, as it looks for a way to compete in global markets. “We cannot compete on a low-cost model and need such innovative approaches. That is why we are proposing Industry 4.0 as an innovative solution.”
New levels of interconnectivity
The key
characteristics of the new industrial landscape are already
being mapped out, says Frank Steffen, also a partner at
Roland Berger. Cyber-physical systems will link the
marketplace and consumer demand with the manufacturing base,
with IT systems built around machines, storage systems and
raw materials inputs.
Smart robots and machines will be able to adapt, communicate and interact with one another and with humans, using remote control. Big Data will bring new ways to handle and analyse huge amounts of market and manufacturing data, to improve supply and demand and scheduling.
New levels of connectivity between the digital and real worlds will enable constant exchange of information between machines, work pieces, systems and humans.
Ultimately, says Steffen, Industry 4.0 has the potential to decentralise a lot of manufacturing and energy consumption, as smaller scale automated facilities can be located closer to essential raw materials or the customer. These may use renewable resources for energy production, such as solar energy or wind energy.
Says Checker: “Industry 4.0 implies a complex, interconnected global system linking big data and cloud computing, with advanced manufacturing systems and supply chains and resources of the future to enable mass customisation of output.”
German task group reports
So what is
the situation at present in the
development of such smart
factories? A lot of work has been done in recent years in
Germany, to set out the concept and implications. In early
2012, the German government set up a working group on
Industry 4.0, under the chairmanship of Siegfried Dais of
Bosch and Henning Kagermann, president of acatech, Germany’s
National Academy of Science and Engineering.
The working group issued its findings in April 2013 at the Hannover Fair, with recommendations for implementing a strategic Industry 4.0 initiative. The group included experts in information and communication technologies, production research, and user industries and was tasked with analysing how the Internet of Things – interconnected smart consumer and industrial devices and products – will affect production and logistics in the future.
The group expects that in the future, “businesses will establish global networks that incorporate their machinery, warehouse systems and production facilities in the shape of cyber-physical systems… capable of autonomously exchanging information, triggering actions and controlling each other independently.”
The chemical industry may not be in the first wave of Industry 4.0, as much of its manufacturing is continuous and oriented around single products from huge dedicated plants. There is already a high level of automation and installed process self-control on such plants, but flexibility of production and inter-connectivity with input supply chains right down to the customer/market are not prime considerations.
But in the specialty areas, where batch processes and formulation are more common, and the manufacturer is closer to the end consumer, then there is potential, believes Steffen. He cites the crop protection as one sector that may benefit from the integration of big data and manufacturing.
Production cycles have always been matched to regional planting seasons and weather conditions, but with the advent of big data to manage knowledge on the weather and soil conditions as well as farmer activity, there is the potential to manage production cycles much more accurately. “Producers will be able to offer new value-add services and increase customer loyalty, as well as gain competitive advantage by better understanding application behaviour.”
An indication that this thinking is already taking hold is offered, says Steffen, by the move in October last year by crop protection and seed company Monsanto to pay $930m to acquire The Climate Corporation, a data company specialising in weather data and simulations.
The acquisition, explained Monsanto, “is expected to expand on The Climate Corporation’s leadership in the area of data science, which represents the agriculture sector’s next major breakthrough, and will immediately expand both the near- and long-term growth opportunities for Monsanto’s business and Integrated Farming Systems platform.”
DuPont too is active in this intensive data area, and earlier this year announced an innovative collaboration with the University of Missouri and the US Department of Agriculture-Agricultural Research Service (USDA-ARS) to pool soil mapping resources, predictive technologies and expertise to help growers more sustainably improve crop yields through better nitrogen application management and other field input planning.
Says Steffen: “The agchem market is characterised by a highly fragmented customer market and a small number of major producers who want to interact with farmers directly. By using soil and weather data they can not only serve the customer better and improve crop yields, but also improve their manufacturing system by feeding this information into planning and operations.”
In effect the agchem business becomes service providers, not just chemical and seed sellers. But the information can also be used to improve formulations and the production footprint. Maybe, he says, companies will review their production base to see if they can use more local, smaller scale capacities, and look at the supply chain to improve efficiencies in delivery.
The same can apply in other areas of the chemical industry, says Checker – maybe the paints and coatings sector, heavily reliant on formulation of hundreds of local products across the globe, or perhaps polymer compounding, where flexibility and customisation is a key requirement.
“The challenges are there”, says Checker, “but we at Roland Berger feel the whole concept around Industry 4.0 resonates well and should play an important role in the wider chemical sector. The industry is of course a key manufacturer and supplier to most other manufacturing sectors.”
F3 factory proves it has the
answers
The chemical industry has already been
involved in a large EU-sponsored public-private initiative to
develop the factory of the future, which its terms the F3
factory – for flexible, fast and future production processes.
The project, part of the SusChem initiative, was initiated in June 2009 and ended in July 2013, with an overall budget of €30m, of which €18bn was provided by the EU’s FP7 innovation programme.
The main facility is the INVITE demonstration unit founded jointly by TU Dortmund University and Bayer Technology Services and located at Chempark in Leverkusen, Germany. This is an open research facility for developing and demonstrating future manufacturing technologies in the chemical sector.
Major chemical producers active in the F3 Factory project include BASF, Bayer, Evonik, Arkema, Rhodia (now part of Solvay), AstraZeneca and Procter & Gamble. Other partners include universities and technology institutes.
The F3 Factory project successfully developed and demonstrated radically new “plug and produce” modular production technology in seven case studies. It was possible to show from an environmental and resource efficiency point of view that drugs, polymers and surfactants can be produced with energy consumption reduced by up to 30%, solvent reductions of up to 100%, a footprint reduction up to 50%, and the potential to reduce or eliminate transportation by enabling local or point-of-use production.
Global News + ICIS Chemical Business (ICB)
See the full picture, with unlimited access to ICIS chemicals news across all markets and regions, plus ICB, the industry-leading magazine for the chemicals industry.
Contact us
Partnering with ICIS unlocks a vision of a future you can trust and achieve. We leverage our unrivalled network of industry experts to deliver a comprehensive market view based on independent and reliable data, insight and analytics.
Contact us to learn how we can support you as you transact today and plan for tomorrow.
READ MORE
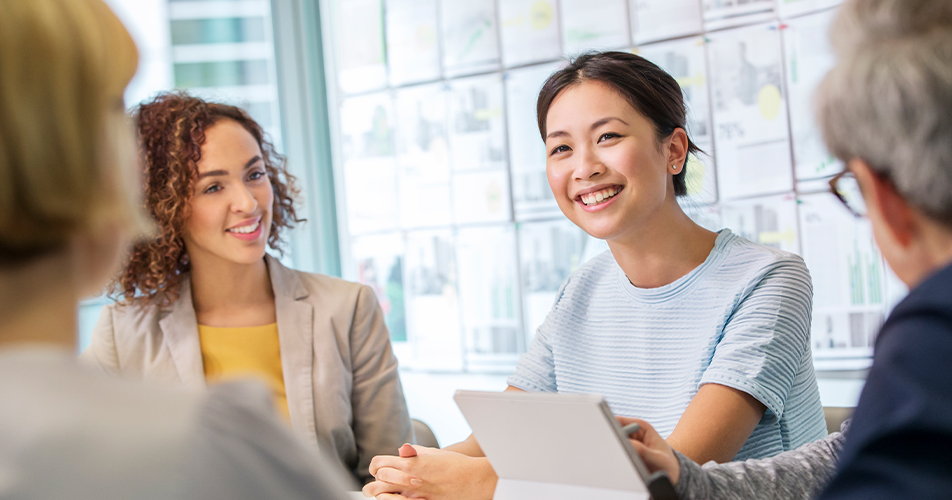