EPCA ’15: Shifting flows spur investment
Elaine Burridge
03-Oct-2015
Focus article by Elaine Burridge
BERLIN (ICIS)–Globalisation and shifting trade flows are having a major impact on Europe’s chemical logistics infrastructure.
Producers, storage terminal operators and transport and logistics companies are all aligning their current and future investments with projections for increasing imports of feedstock as well as chemicals and polymers.
Dow Chemical has two major projects under way that are having a significant effect on its supply chain. These are the Sadara Chemical project in Saudi Arabia, a joint venture with Saudi Aramco which includes 26 world-scale petrochemical plants; and ethylene, propane dehydrogenation (PDH) and PE plants in Freeport, Texas, on the US Gulf Coast.
Peter Marshall, logistics director for Europe, Middle East and Africa and India (EMEAI) at Dow Chemical, and also a member of the EPCA’s supply chain programme committee, says the company’s present focus is on investing in the logistics and infrastructure required to bring product from these plants to the market.
Nearly 3m tonnes/year of material will come on stream at the Sadara complex in Jubail, Saudi Arabia, within the next 12 months. Ethylene and initial polyethylene (PE) production will begin in the second half of 2015 followed by ethylene oxide/propylene oxide (EO/PO) and derivatives, with polyurethanes (PU) in the final phase due by the end of 2016.
Dow Chemical’s intention is to sell material predominantly into growth regions, not necessarily into western Europe, but mainly to new markets such as Africa, says Marshall. Supply chain design started at the same time as the two complexes’ engineering developments, and discussions with logistic service providers (LSPs) began more than two years ago.
“There are numerous locations around Europe where tank terminal operators are building facilities on our behalf and expanding their capability, some with warehouses,” Marshall says, adding that roughly two-thirds of Sadara’s output will be packed in various forms and handled through warehouses. He explains that Dow’s focus is to bring downstream products such as PE to the market rather than raw materials. Late last year, Andrew Liveris, Dow Chemical’s CEO, ruled out pursuing US exports of shale-derived ethane for its European operations, claiming that liquefied petroleum gas (LPG) offers a higher-margin alternative.
The company has flexible cracker operations and in recent years has increased the ratio of LPG to naphtha in its feedstocks. It has invested in expanding LPG cracking at Tarragona, Spain, and can crack LPG at its facility in Terneuzen, the Netherlands. Additional investment in strengthening its European LPG infrastructure has continued in 2015.
Several companies, including INEOS, SABIC and Borealis, are making plans to import ethane derived from US shale gas. INEOS’ plans are well advanced and approximately 800,000 tonnes/year of US ethane is being delivered to its 560,000 tonne/year cracker in Rafnes, Norway, where a new storage tank and terminal have gone into operation.
At Grangemouth, UK, INEOS is building what is said to be Europe’s largest ethane storage tank with a capacity of 60,000 cubic metres, as well as an import terminal. First shipments of US ethane are expected to arrive in Grangemouth during the second half of 2016.
The company has also commissioned the construction of eight dragon-class ships which have the option to transport LPG, liquefied natural gas (LNG) as well as petrochemical gases including ethylene.
SABIC Europe is modifying its 865,000 tonne/year cracker in Wilton, UK, to operate on US-sourced ethane. The upgrade is scheduled to be completed during 2016.
Borealis signed a 10-year deal with US shale gas producer Antero Resources to supply 240,000 tonnes/year of ethane to its 625,000 tonne/year cracker at Stenungsund, Sweden starting next year. It is investing €120m in logistics and in an upgrade of the cracker.
Meanwhile, Italy’s Versalis, which was understood last year to be reviewing the case for using ethane at its cracker in Dunkirk, France, has yet to confirm a decision. Its ethane project remains open, the company says.
With regard to investments for rising imports of LNG, Otto Schulz, partner at global management consultancy A.T. Kearney, says facilities are already available in preparation for imports from the Middle East and these could also be used for imports from the US.
He says the focus is on investing in the UK and southern Europe, with the possibility of more terminals being established in mainland/northern Europe. Experimental loads of LPGs are moving into Spain, the UK and Scandinavia too.
“Europe is looking to import advantaged LPG and naphtha/condensate and possibly in Iberia/the Mediterranean for ethane,” he says.
In order to serve the region’s rapidly changing trade flows, Swiss transport and logistics provider Bertschi has been expanding its chemical hubs in major European ports, building storage areas for imports of hazardous chemical products and developing value-added solutions.
Perhaps the most significant investment in recent times is in its chemical logistics hub in Schwarzheide, Germany, which CEO Hans-Joerg Bertschi describes as “the market leading gateway for intermodal chemical product flows between western Europe and eastern Europe/Russia.”
The expansion at Schwarzheide, which cost around €15m ($17m), added a second crane runway with six rail tracks as well as a gantry crane, and offers extra capacity to meet rising demand for storing hazardous goods containers.
Bertschi says the launch of the dangerous goods storage bridged a gap in the region. Container handling capacity has been doubled to 120,000 TEU (20-foot equivalent unit), and storage capacity has tripled to 2,400 TEU. Plans exist to further extend logistics services at the hub.
Following the investment, Schwarzheide now offers connections on Europe’s northsouth axis, in addition to its traditional westeast links. The hub now has direct access to the deep-sea ports of Hamburg and Bremerhaven in Germany, and new connections to Slovakia (Dunajska Streda) allow intermodal shipments to Slovakia, Hungary, Romania and Istanbul in Turkey.
Bertschi is also planning to make significant investments at its other hubs too. “We plan to double the storage and handling capacity of the import/export of hazardous chemicals at our Botlek terminal in Rotterdam and to build new dangerous goods storage infrastructure in Duisburg, Germany, integrated in our trimodal rail terminal.” These expansions will take place next year.
The company is also investigating possibilities for further investments in value- added logistics at other European terminal locations.
According to Bertschi, demand for intermodal rail has picked up significantly this year. Demand for chemicals is much more robust than a year ago, he says, and Europe’s competitiveness has greatly improved as a result of the weakening euro. However, he notes that intermodal capacity is limited and some bottlenecks are developing.
“There is a trend to move especially hazardous products to rail and go for intermodal as much as possible,” says A.T. Kearney’s Schulz, who mentions also Europe’s reliability issues resulting from bottlenecks, for example in the Rhine valley.
For industry to respond effectively to capacity bottlenecks, Bertschi believes that digitalization of the supply chain will help contribute to better utilisation of existing infrastructure.
“Major chemical logistics operators like Bertschi invest growing sums into IT to achieve a better visibility, more robust planning and a stronger resilience of current supply chains. These are the low-hanging fruits to cope with logistics bottlenecks,” he says.
In addition, advanced chemical logistics operators will continue to invest significant amounts into innovative solutions. The use of waterways, smarter technologies enabling higher railway infrastructure utilisation and new consolidation hubs are just a few examples that Bertschi highlights.
One major issue mentioned by both Schulz and Dow Chemical’s Marshall is Europe’s ageing and deteriorating infrastructure. Both cite Germany, where there has been a big focus in the past couple of years to fix and replace old infrastructure such as bridges that have been hindering chemical transportation. One example is the Leverkusen Bridge on the river Rhine, which has been undergoing construction and patchup work since it closed in 2012 because of the wear and tear from heavy traffic.
“There have been some fairly alarming figures about the number of bridges needing repair over autobahns and trucks being diverted on a frequent basis. This has been the same for rail and inland waterways,” says Marshall.
According to a recent report by the German Institute for Economic Research, 46% of bridges, 41% of streets and 20% of highways are in need of repair.
Marshall comments: “We are being handicapped by the continued growth in traffic particularly on the east-west axis as eastern Europe has developed.”
He says that 80% of Dow’s shipments from northern Europe to Italy are intermodal but there are still plenty of opportunities to do more, particularly on the east-west axis.
He concedes that it requires a lot of collaboration from different parties, and sharing with LSPs and key partners, but emphasizes that companies and governments in Europe need to develop these options.
The full version of this article was published in ICIS Chemical Business in a special feature prepared for the 49th EPCA Annual Meeting 2015. It can be seen by clicking here. For more information and articles from ICIS at EPCA 2015 click here.
Global News + ICIS Chemical Business (ICB)
See the full picture, with unlimited access to ICIS chemicals news across all markets and regions, plus ICB, the industry-leading magazine for the chemicals industry.
Contact us
Partnering with ICIS unlocks a vision of a future you can trust and achieve. We leverage our unrivalled network of industry experts to deliver a comprehensive market view based on independent and reliable data, insight and analytics.
Contact us to learn how we can support you as you transact today and plan for tomorrow.
READ MORE
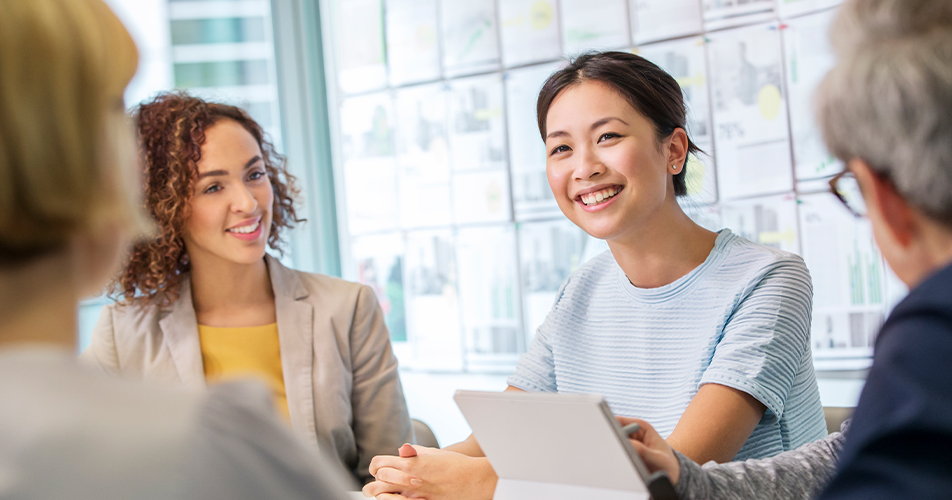