Higher PP margins may spur more US plants
Al Greenwood
30-Oct-2015
HOUSTON (ICIS)–A
rise in US margins for polypropylene (PP) could encourage
more companies to consider expanding production of the resin
in North America.
Goradia Capital, the owner of distributor Vinmar, became the latest to consider building a new PP plant.
Earlier this week, it signed a deal to buy 450,000 tonnes/year of propylene from a propane dehydrogenation (PDH) unit that Williams may build near Edmonton in Canada’s Alberta province.
Goradia would use the propylene to make homopolymer PP on the same site as Williams’s PDH unit.
In addition, Formosa Petrochemical is studying the feasibility of building a PP plant in Louisiana, part of a larger project that would also include ethylene derivatives.
The company did not specify the size of the plant.
A sister company, Formosa Plastics, said it will build a new PP plant at its complex in Point Comfort, Texas. It also did not reveal the capacity.
In April, Braskem America CEO Fernando Musa said the firm was studying a new plant as well as debottlenecking options at its five existing US PP sites.
If any of the companies pursue the projects, it would mark the first time in years that a company has built a new PP plant in North America.
Until recently, US companies had been shutting down PP plants.
In 2009, Sunoco said it would shut down and dismantle its 200,000 tonne/year PP plant in Bayport, Texas.
Phillips Sumika announced in 2011 that it would shut down its two PP units in Pasadena, Texas, which had a total capacity of 365,000 tonnes/year.
Initially, the advent of shale gas made PP plants even less desirable as it caused crackers to favour lighter feedstocks. Lighter feeds produce less propylene.
Consequently, propylene supplies tightened. Prices for the monomer rose well above those for ethylene, breaking a historic trend.
“When the monomer availability didn’t keep up, it got a little pricey,” said John Jones, a plastics consultant. “That slowed things down a bit.”
However, the outlook for PP began to improve.
On the demand side, the US automobile industry recovered from the recession. Automobiles already use a lot of the resin, and they are using even more to lighten the weight of their vehicles.
PP is the lightest resin among the commodity plastics, and the weight savings are helping automobile manufacturers comply with ever stricter fuel-efficiency standards, said James Ray, senior consultant for ICIS.
Given the recovery in the US, PP demand has exceeded supply, he said.
As a result, the net trade balance for US PP has reached its lowest levels since at least 2010, Ray said. Plant utilisation rates are in the high 80s, making it difficult for companies to increase PP production further.
On the feedstock side, propylene prices have fallen because of the decline in oil and because of rising supplies.
Propylene supplies increased in part because of higher refining rates. Refineries make propylene as a by-product in their fluid catalytic crackers (FCCs), and production of the monomer increased as a result of the higher rates.
Crackers also began using heavier feedstock, in reaction to lower propane and butane prices. These feedstocks produce more propylene.
Increased production pressured propylene prices lower, improving the economics of making PP.
US naphtha-based PP margins now stand at 21 cents/lb ($463/tonne), up from 8.95 cents/lb in 2014, Ray said. Margins in 2013 were even lower, at 4.56 cents/lb.
Margins for PP producers integrated with PDH units are even higher, at 30 cents/lb, Ray said.
The PDH figure is largely hypothetical, since the US currently has no PP plants integrated with such units, Ray said. However, it shows how PP producers could benefit if their operations were integrated with PDH plants.
An upcoming wave of new PDH plants could make such high margins a reality.
Formosa Plastics is building its PDH unit in the same complex as its new PP plant in Texas. The two could be integrated.
The Williams and Goradia plants could operate as an integrated unit.
Braskem Americas could achieve some of the benefits of integrated margins if it signs a long-term supply agreement with one of the new PDH operators.
As it is, Enterprise Products will sell the propylene from its PDH unit to other companies.
The US may also attract a foreign company that would build an integrated PP complex through a joint venture, Ray said. If the company could find a domestic partner, it would be easier to enter the US market than if it built the new plant by itself.
However, the likelihood of any new PP plants in the US will depend in part on propylene margins. That, in turn, will revolve around the prospects of new supply.
Recently, the drop in oil prices have made PDH units less attractive, and some companies have called off their plans.
In addition, PDH plants are expensive to build and difficult to start up, Ray said.
Focus article by Al Greenwood
(Image: ZUMA/REX Shutterstock)
Global News + ICIS Chemical Business (ICB)
See the full picture, with unlimited access to ICIS chemicals news across all markets and regions, plus ICB, the industry-leading magazine for the chemicals industry.
Contact us
Partnering with ICIS unlocks a vision of a future you can trust and achieve. We leverage our unrivalled network of industry experts to deliver a comprehensive market view based on independent and reliable data, insight and analytics.
Contact us to learn how we can support you as you transact today and plan for tomorrow.
READ MORE
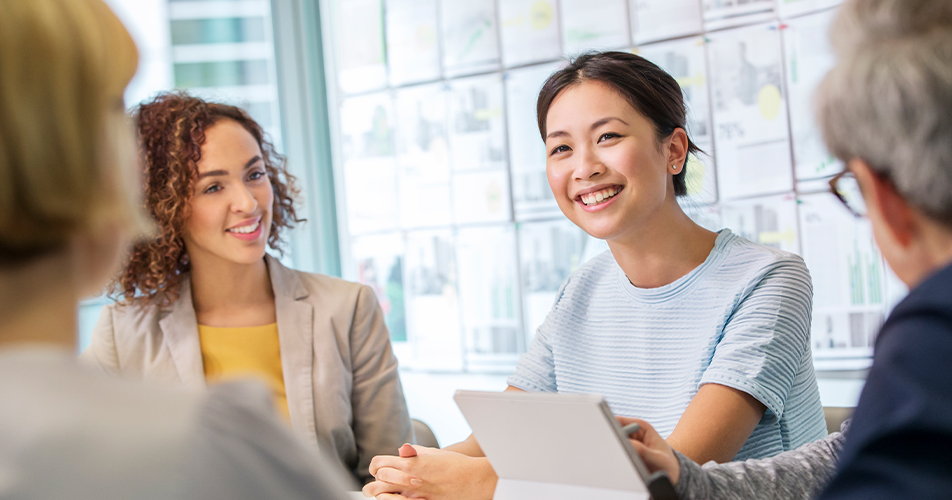