Carbon fibre will drive demand for automotive chemicals
Will Beacham
16-Dec-2015
LONDON
(ICIS)–Demand for automotive chemicals could grow
significantly over the next 5-10 years if the adoption of
carbon fibre for automotive manufacture becomes more
widespread, according to manufacturer Cytec.
As legislation pushes automotive manufacturers to reduce vehicle weight and cut emissions, original equipment manufacturers (OEMs) – especially in the luxury market – are turning to carbon fibre as a lightweight alternative to aluminium and steel, says Alexander Aucken, global automotive manager for the US-headquartered company which merged with Belgium’s Solvay earlier in December.
The move from steel to aluminium in automotive design has not reduced emissions to the levels required by legislators so OEMs are now investigating the use of carbon fibre composites anywhere in the vehicle to reduce weight. This can be in the primary structure (the main body of the vehicle) or secondary structure (crash systems, bulkhead, engine frame) which are not part of the main frame but add significantly to vehicle weight.
Aucken says there is a huge amount of work going on with OEMs to make carbon fibre materials compatible with automotive design. For this a more rapid production cycle time is required than the current three-to-four hours it takes to produce a part using traditional autoclave (pressure and heat in an oven) techniques.
“This is very effective for low-volume parts but if you are making 20,000-50,000 vehicles a year you may need that process to change to have a significant impact on reducing the cost and cycle time to make a part. With a four hour cycle time you would need hundreds of tools for high volumes. Therefore composite materials have been developed which can reduce cycle times to three minutes or less.”
Cytec is working with Jaguar Land Rover and an engineering consulting company on research and development which aims to improve understanding of the requirements of OEMs and how carbon fibre can be modified to suit their needs. The OEMs, on the other hand, want to find out how to balance design, manufacturing processes and materials as they move towards the use of carbon fibre.
In December 2015, Cytec opened a $13m application centre at Heanor, UK, which will allow it to work with partners on introducing new rapid cure thermoset prepregs (reinforcing fabrics) and resin systems into a high-volume production setting.
“We understand the materials but we also want to understand how they are processed so that we can adapt the materials to allow them to be processed better and faster. We have opened our application centre with that in mind. We don’t want to make parts. But to supply materials we need to understand how to make parts,” says Aucken.
Not all OEMs need carbon composite parts for weight reduction, according to Aucken. High volume manufacturers have already been effective in lowering vehicle weight so don’t need to focus so much on further weight reduction. But Jaguar Land Rover, BMW, Daimler and other luxury brands still need to reduce weight and emissions.
A standard steel chassis of a car can weight 300-350kg but by using a composite design this can be reduced to 120-130kg. The first mainstream production car to use a composite chassis was the BMW i3 a couple of years ago. “I would expect this to be adopted more widely over the next 5-10 years,” says Aucken.
Consultants CarbConsult forecast that carbon fibre use in the automotive sector could grow from 9,000 tonnes/year in 2011 to between 30,000 and 230,000 tonnes/year by 2022.
Cytec manufactures its own carbon fibre. The polyacrylonitrile (PAN) precursor is transformed into carbon fibre by spinning, stretching and heating. The fibres are blended with epoxy resins, vinyl esters or other thermoset chemistries to produce pre-impregnated rolls which can be cut to shape.
Aucken believes chemical feedstock requirements will be very significant for the automotive supply chain over the next 5-10 years.
“This supply chain needs to be secured to ensure that risks are managed carefully. Work is going on to ensure this is put in place with plant, equipment and cost models to ensure that there is a guaranteed supply of these materials. We have a lot of relationships with the chemicals and materials supply chain to ensure we will have the volumes we will need for high volume, lightweight manufacture.”
OEMs will need to design their vehicles for composites as they progress beyond the use of steel.
He says: “There is a continuum of development from steel to aluminium and now on to composites. The benefits of composites will become obvious and will be accepted for performance reasons. The luxury market will adopt composites first but when the benefits are known who knows [how deeply composites could penetrate the OEM market]?”
Aucken believes that 3D printing is a fascinating technology which Cytec and the OEMs are examining though it will require a large amount of technological development.
Commentators suggest 3D printing could revolutionise the automotive supply chain. Spare parts could be ordered, printed and distributed locally, reducing the need for a long supply chain and cutting working capital requirements for inventory.
“It’s a hugely exciting opportunity. We have a 3D printer and are mixing thermoplastic resins with carbon fibre for use in 3D,” said Aucken.
Interview article by Will Beacham
Image source: Cytec – Carbon fiber reinforced door inner structure, manufactured from a filament wound flat.
Global News + ICIS Chemical Business (ICB)
See the full picture, with unlimited access to ICIS chemicals news across all markets and regions, plus ICB, the industry-leading magazine for the chemicals industry.
Contact us
Partnering with ICIS unlocks a vision of a future you can trust and achieve. We leverage our unrivalled network of industry experts to deliver a comprehensive market view based on independent and reliable data, insight and analytics.
Contact us to learn how we can support you as you transact today and plan for tomorrow.
READ MORE
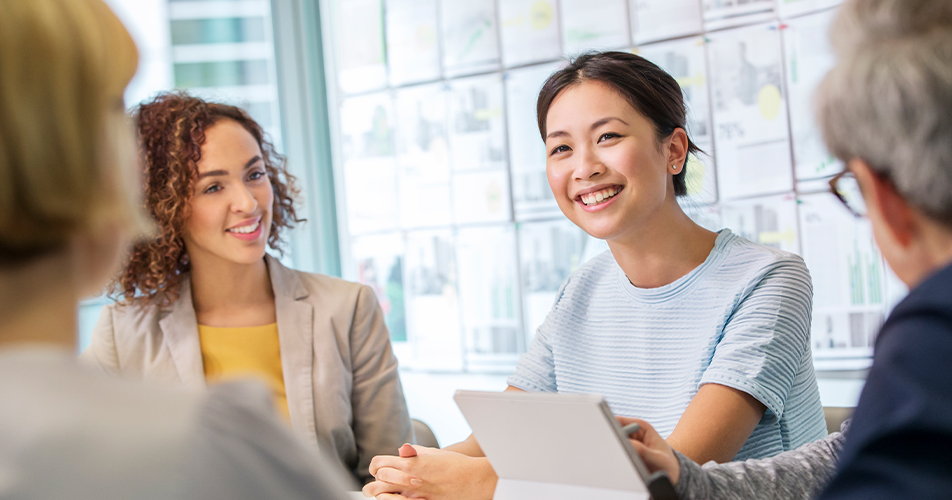