Asahi Kasei finds phosgene-free route to polycarbonates
14-Oct-2007
CORRECTED: Corrects spelling of Kazan Organsyntex to Kazanorgsintez paragraph 6 and polycarbonate capacity in paragraph 9 to 300,000 tonne/year
After 30 years of development, a company has come up with a way to manufacture this clear plastic without producing highly toxic by-products
John Baker/London
ASAHI KASEI Chemicals must be running out of wall
space as a result of all the awards it has received in
recognition of its development of a phosgene-free route to
polycarbonates (PCs). Let’s hope it has space for the ICIS
Process Innovation Award, too!
The new process, the development of which began in 1977, uses three raw materials – ethylene oxide (EO), carbon dioxide (CO2) and bisphenol A (BPA) – which are converted to PC and high-purity ethylene glycol (EG), without any waste or waste water. The technology is based on recycle-type reactive distillation methods to produce the intermediate monomer, and a new gravity-based non-agitating unit equipped with vertical glides for the polymerization.
A phosgene-free route to PCs has been a long time coming, with a number of producers seeking to overcome the inherent problems related to the process. Not only are phosgene and the other raw material, methylene chloride, highly toxic, but the process generates large quantities of wastewater and PC with chlorine impurities.
Shinsuke Fukuoka, who, along with Kyosuke Komiya and Shigenori Konno is credited with the development, notes that there were significant barriers to develop the phosgene-free route. These included developing an economical process technology to produce the safe monomer diphenyl carbonate (DPC) with sufficient purity, and the polymerization technology to remove by-produced phenol from the ultrahigh-viscosity molten prepolymer.
But Asahi cracked both problems. The first step of the process sees DPC produced from phenol and dimethyl carbonate – both recycled within the process. The reaction and distillation steps are carried out simultaneously in the same column. The breakthrough in polymerization came in the design of a gravity-based, nonagitated vertical reactor, fitted with guides. This gives relatively stable and efficient production.
After bench work began in 1986 and pilot-scale development in 1988, the process was commercialized in 2002 with a 65,000 tonne/year facility built by Chimei-Asahi in Taiwan. It is now used at a second, 75,000 tonne/year facility of that joint venture, and has been licensed to Kazanorgsintez in Russia. Three companies have licensed it, with start-ups expected from 2008-2010.
Asahi Kasei has a policy to license the technology openly because of the contribution it makes to society – it expects 25% of total world production of the polymer to be based on its process within the next few years. PC, the largest-volume engineering plastic, with a market of 3m tonnes/year, is expected to grow at 10%/year.
Asahi says a plant based on the process costs around half the traditional cost of phosgene-based units. It adds that production costs are also lower because the raw materials are cheaper, more products are recycled within the process and the resultant PC is purer.
Fukuoka says: “Although the polycarbonate resin market was small – about 300,000 tonnes/year when we started the basic research – the market was expected to grow because the resin has excellent properties such as good transparency and impact resistance.” He was eager to develop an innovative process for producing PC to replace the phosgene process that was the only commercialized route.
Asahi Kasei employs about 2,000 people and invests around $444m (€316m), or 3.2% of net sales in 2006, in research. Fukuoka adds that from its history the company has possessed “a DNA which encourages researchers and engineers to challenge and innovate in extremely difficult subjects.” He adds that from the early 1980s the R&D administration of the company took a keen interest in developing environmentally friendly technologies. “We intended to replace this phosgene process, which was not environmentally friendly, with one that was.”
And that process has not stopped. Fukuoka notes that work is continuing to further refine and develop the technology – especially to improve productivity and energy consumption. He adds that the process can be adopted for polycondensation polymerization reactions in general. Developments for producing polyethylene terephthalate (PET) and polytrimethylene terephthalate (PTT) have already been completed. And a number of polyester production patents have been filed globally.
For more information on Asahi Kasei, visit www.asahi-kasei.co.jp
Global News + ICIS Chemical Business (ICB)
See the full picture, with unlimited access to ICIS chemicals news across all markets and regions, plus ICB, the industry-leading magazine for the chemicals industry.
Contact us
Partnering with ICIS unlocks a vision of a future you can trust and achieve. We leverage our unrivalled network of industry experts to deliver a comprehensive market view based on independent and reliable data, insight and analytics.
Contact us to learn how we can support you as you transact today and plan for tomorrow.
READ MORE
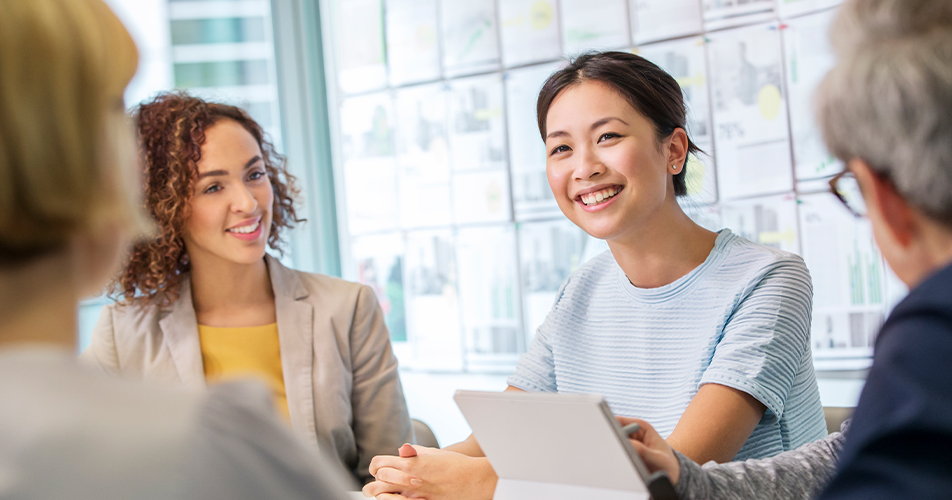