Sports is a key market for carbon fiber
17-Aug-2009
Sporting goods are often a test bed for new carbon fiber composites
Cynthia Challener/Vermont, US
ATHLETES AND sportsmen today expect continual improvement in the performance of their equipment. Manufacturers of sporting gear have risen to the challenge, not only by refining their designs, but also by incorporating innovative materials. Among the most successful of these have been carbon fiber composites.
Sporting goods and recreational equipment account for 18-20% of the carbon fiber market, which Lucintel, a US-based market research firm, estimates was worth $1.5bn (€1bn) in 2008. The balance comes mainly from two other sectors: aerospace and commercial/industrial.
Worldwide volume now stands at about 35,000-40,000 short tons (35,500-40,600 tonnes), according to one manufacturer.
The value of the global carbon fiber market has grown at double-digit rates over the past five years, says Lucintel, but growth will decline to just 1.8%. Commercial aerospace and wind energy are proving to be the only bright spots.
Lucintel expects a return to higher growth rates for 2010, and by 2014, the market is expected to reach $2.4bn.
Demand from the sporting goods/recreational sector is expected to grow at a compound annual rate of about 3% from 2007 through 2014.
The complexity of the production process (see box) has kept the number of carbon fiber producers in the market to relatively few – under a dozen, in fact. Leading players include Cytec Industries and Hexcel, both US-based, and Japan-based Mitsubishi Rayon, Toho Tenax and Toray.
“Over the last 30 years, we have developed an extensive amount of process knowledge, which has been necessary for production of high-quality, high-performance materials,” observes Steven Carmichael, director of sales and marketing at Grafil, a wholly owned subsidiary of Mitsubishi Rayon. “The need to have this level of experience definitely serves as a barrier to entry into the marketplace.”
Ongoing development focuses on delivering uniform product quality within a cost-sensitive production system, according to an official at a US manufacturer. “The emphasis is on reliability, so that end-product fabricators know the expected range of fiber properties and can design their products, including sporting equipment items, accordingly,” he states.
KEY CHARACTERISTICS
Important
properties include fiber yield (mass per unit length),
uniform sizing content and processing characteristics such as
low fuzz or even tow (filament band) spreadability. Carbon
fiber manufacturers can control the fiber’s tensile strength
and tensile modulus (resistance to bending) – the two key
properties of interest to end users – in the selection of
precursor materials and the processing conditions under which
the carbon fiber is made. These developments are the direct
result of the collective need of the advanced composites
industry.
Sporting equipment manufacturers need assurance that their raw material suppliers have their manufacturing process under control and can deliver a product with consistent values and properties. Customers are also always looking for a new feature or performance characteristic that can be marketed in turn, to their own customers.
Recent product innovations have included modifications to the carbon tow geometry such as flatter band width to help companies make thinner, or lighter pre-impregnated intermediate materials.
These advances benefit all segments of the carbon fiber market, including that for recreational products. Some of the earliest commercial carbon fiber products were first used in the recreational market, and much technology development, process and product improvement effort takes place in this segment, according to Carmichael.
“The recreational market often serves as a springboard for testing new innovations,” notes the official, who spoke on condition of anonymity. For example, some companies introduce new materials to the sporting goods market, where commercialization often occurs much more quickly, in order to develop a large database of performance values that later can be presented to customers in the aerospace market.
“It’s very exciting to see how materials knowledge is transferred to other market segments. In that sense, sporting goods represent a chance to introduce new or modified materials,” he states.
Golf shafts have been the No. 1 sporting application for carbon fibers for many years. Their use in hockey sticks and bicycle frames is increasing, however. Carbon fibers can also be found in rackets, fishing rods, ski poles, snowboards, sailboard masts, marine hulls, backpack frames, tent poles, softball/baseball bats, bowsand arrows. The versatility of carbon fibers stems from the wide variety of composites that can be made from them.
“Composites have characteristics of the resin matrix and of the carbon fibers, and there are many different variations of each of these materials to consider. Then of course there is the interaction between the fiber surface and the matrix. This complexity is the source of the value that carbon fiber brings to sporting goods and its numerous other end-uses,” says Carmichael.
Carbon fiber has made hockey sticks lighter, replaced breakable wooden bats and allowed the creation of 10m-long fishing poles. Golf shafts are often manufactured with two or three different types of carbon fiber materials. Different ply thickness, orientation and even selection of the fiber’s tensile modulus properties are optimized for specific types of club, Carmichael points out.
“With this capability, manufacturers can carefully dial in the dynamic performance, providing both strength and dynamic performance, performance that can be controlled – an achievement that simply is not possible with a homogenous material such as metal,” he says.
Get the latest chemical industry news
A TRICKY PROCESS
Most carbon fiber is
produced by acid-catalyzed polymerization of acrylonitrile to
form polyacrylonitrile (PAN). Following purification, the
powdered PAN is dissolved in a solvent and extruded in a
wet-spinning process to produce thousands of filaments. The
fibers are then washed, dried and stretched on rollers to
orient the polymer chains. After treatment with a finishing
oil, the white fibers are dried and wound onto bobbins.
Conversion from PAN to carbon fibers requires oxidation at 200-300ºC (392-572ºF) followed by carbonization in an inert atmosphere at very high temperatures. The fibers are spread flat into a band of many filaments called a tow. Oxidation, which takes several hours, induces crosslinking and increases the fiber density. Carbonization first occurs at 700-800ºC, with final heating at 1,200-1,500ºC.
Once the fibers are formed, they are treated with sodium hypochlorite, nitric acid or some other chemical to modify their surface and increase reactivity with the resins they will be combined with to form the composite. A coating called a sizing is then applied to protect the fiber. The surface treatment, sizing, and process technology required to produce carbon fiber are proprietary to each manufacturer. Many offer custom solutions to meet the specific needs of customers in different end-markets. The dried fibers are separated into individual tows and wound onto bobbins in preparation for shipment.
At the prepreg (pre-impregnated fiber) manufacturer, the bobbins containing the carbon fiber tows, with 12,000-60,000 filaments each, are placed onto a creel (spindle) so the fiber can be pulled off and fed (150-250 at a time) into a machine that impregnates the fibers with a resin, usually an epoxy, thereby producing the prepreg. This is then partially cured at 121-176ºC to fabricate a composite part of some type. Most carbon fiber composite laminates used in sporting goods equipment are cured at 482ºC.
Global News + ICIS Chemical Business (ICB)
See the full picture, with unlimited access to ICIS chemicals news across all markets and regions, plus ICB, the industry-leading magazine for the chemicals industry.
Contact us
Partnering with ICIS unlocks a vision of a future you can trust and achieve. We leverage our unrivalled network of industry experts to deliver a comprehensive market view based on independent and reliable data, insight and analytics.
Contact us to learn how we can support you as you transact today and plan for tomorrow.
READ MORE
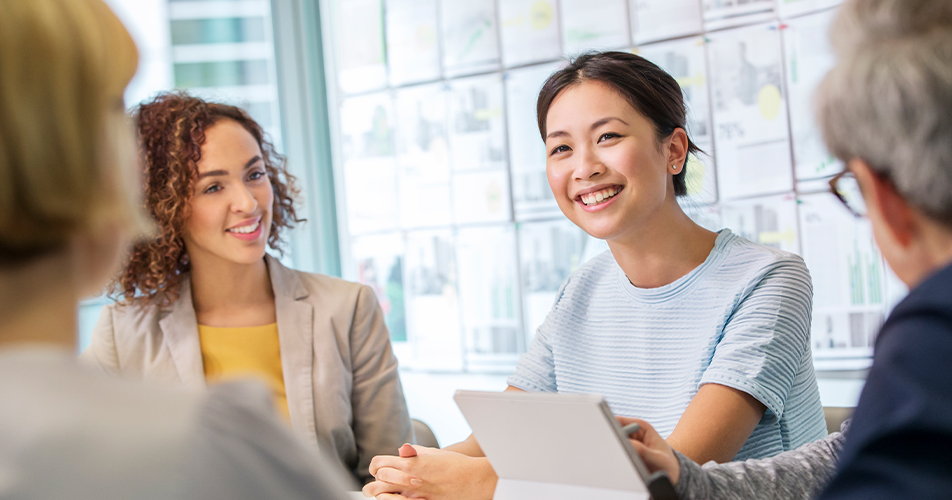