EU chlor-alkali plant conversions not an issue – executive
Janos Gal
12-Mar-2013
By Janos Gal
LONDON
(ICIS)–The phasing-out and conversion of plants using the
mercury production process will not cause shortages in the
European chlor-alkali industry, Alistair Steel, executive
director of Euro Chlor told ICIS.
“Europe will continue to be a strong production base for chlorine and caustic soda for a long time to come, even after the conversion is done,” Steel said in a recent interview.
Euro Chlor represents the European chlor-alkali industry, and Steel has been at its helm since 2006. Prior to that he worked for France-based chemical producer Rhodia, where he was managing director of the company’s UK business for five years.
“If some plants decide to close down, others will increase utilisation rates, so overall output will not drop,” Steel stressed.
Steel discussed points raised in an article published by ICIS, detailing how a recent announcement by the United Nations Environmental Programme’s (UNEP) Mercury Convention could impact the global chlor-alkali industry.
On 19 January 2013, the UNEP passed a set of legally binding measures which were accepted by more than 140 countries.
Members of the convention agreed to a mandatory deadline for the phase-out of mercury cells – used in the production of chlorine, caustic soda and other chlor-alkali products – by 2025. Mercury is a liquid-form metal which is highly toxic.
Chlorine utilisation rates in Europe are currently estimated at 76%. If in the future a plant that cannot afford to convert decides to close down, the remaining plants will increase output.
Thus, overall utilisation rates will go up and the remaining plants will produce the same amount, or more, of chlorine and caustic soda.
“Fewer plants will produce more, at a better efficiency rate,” Steel added.
In contrast, a caustic soda producer in Egypt said that although the remaining plants may be able to increase output, the high toxicity of chlorine restricts its transportation, which means the remaining plants may not be able to supply all areas of Europe.
If a mercury-process chlorine plant that supplied nearby consumers closes down, those consumers may be left without chlorine if the nearest alternative unit is too far away, the producer said.
Chlorine is used in the production of polyvinyl chloride (PVC), epichlorohydrin (ECH) and polyurethane (PU), and in the manufacture of pharmaceuticals.
In Europe chlorine is generally transported to distances not exceeding 400-500km (249-310 miles) from a production unit, according to industry sources.
For example, if a truck overturned and chlorine leaked it would corrode everything in the surrounding area. If chlorine reacts with air chlorine gas is created – breathing it burns the lungs, which can be lethal. Hence, transportation over long distances is not recommended for safety reasons.
The European industry agreed a voluntary deadline separately before the UNEP measures to convert all mercury process plants by 2020.
According to Euro Chlor, of the three chlor-alkali processes the mercury process uses the most electricity. In addition, at the end of the chlor-alkali process mercury must be removed from the hydrogen gas and caustic soda solution.
In Europe, the 34 mercury-based chlorine plants active in early 2012 will need to be converted to a more energy-efficient non-mercury process.
At that time plants using the mercury process accounted for about 31% of European chlorine production capacity, while the alternative diaphragm cell process accounted for 13% and the membrane process for 53%. The remaining 3% is accounted for by other processes, Euro Chlor’s latest data shows.
“By converting to the membrane process, a mercury-based production unit can save 25-30% of electricity, but this gain is partially offset by an increase in steam consumption,” said Jean-Pol Debelle, technical director at Euro Chlor.
The possible closure of some of these plants does not mean the European market will become tight, Debelle added.
“As these operations will be done progressively it will not have a major impact. It has been happening [in the EU] and other parts of the world for several years now without any such problems, so we don’t expect any impact in Europe,” Debelle said.
Some sources offer different viewpoints, however: “Not everyone will be able to afford the conversion process and inevitably there will be victims of this recent push to modernise the industry,” said a producer in the chlor-alkali chain, which preferred to remain anonymous.
“It costs hundreds of millions of euros to convert a plant, and in the current economic climate it is unlikely anyone will be willing to invest such huge amounts of money,” the producer added.
Euro Chlor estimates it will cost €2bn ($2.6bn) to convert the remaining mercury process plants in Europe.
Another factor that concerns European producers is high energy costs. Industry players in the US have a huge cost advantage resulting from cheap, shale gas-derived energy.
Energy costs are a big worry as they are much higher in the EU than in the US – where shale gas makes energy a lot cheaper – so there is a competitive disadvantage in the EU, Euro Chlor’s Steel said.
It is estimated that it costs about $200 (€154) per electrochemical unit (ECU) more to produce the equivalent amount of chlor-alkali products in the EU than in the US. This is mostly down to cheaper shale gas and more “industry friendly” taxation and legislation, Steel added.
“The EU industry is hampered by high energy costs – we are being shackled, and this is a major drag on the industry’s competitiveness,” he added.
Steel also referred to the EU’s Emissions Trading System (ETS), which is leading to a significantly increased environmental cost burden on the industry.
“We need new policy to lower the price of energy. The chlorine and caustic industries are under huge pressure now, but it is a well managed industry and it will pull through the hard times,” he said.
Not everything is doom and gloom, however. In Europe, Dutch paint producer AkzoNobel announced in 2011 it would upgrade its chlorine plant in Frankfurt from 165,000 tonnes/year to 250,000 tonnes/year by the fourth quarter of 2013, using the membrane process.
Also, Germany-based Leuna Tenside started up two new 15,000 tonne/year units last year, while Italy-headquartered Altair increased its production capacity by 30% in 2011, Euro Chlor said.
There are also several new plants coming online in 2013-2025 globally, adding more than 1m tonnes of capacity in 2013 alone (see table).
Caustic soda sales are mostly influenced by demand from the downstream alumina, soaps and detergents and pulp and paper industries.
As a result of the global macroeconomic slowdown, demand for these products has dropped significantly, caused by falling output in the automotive and construction industries in particular.
Sales to the alumina sector, the largest caustic soda consumer, are extremely poor, and this resulted in several alumina plant shutdowns.
Among others, US-based Alcoa announced in early 2012 that it would close several of its alumina units. This was followed by Russian major Rusal later in 2012, which shut down its unit in Friguia, Guinea because of poor market fundamentals.
The Friguia plant could restart in mid-2013 if the right market conditions exist, a company source said.
In Europe, the chlor-alkali chain was hit hard by the economic crisis and plummeting demand from the automotive and construction industries, where most chlor-alkali derivatives are used.
This resulted in falling income for chlor-alkali producers, and the need to rationalise. In light of this, there are a number of industry sources that think not all producers will go ahead with the conversions.
However, Debelle was optimistic: “Shutdowns and closures are not really the issue, what is more worrying is the high energy costs. The industry will convert progressively.”
New caustic soda units in 2013 | |||
Plant |
Location |
Estimated capacity |
Opening |
Akzo Nobel |
Frankfurt, Germany |
250,000 tonnes/year |
Q4 2013 |
Aditya Birla Chemicals |
Renukoot, India |
52,000 dmt/year |
Q1 2013 |
Asahimas |
Indonesia |
110,000 dmt/year |
Q1 2013 |
LG |
South Korea |
270,000 dmt/year |
Q1 2013 |
Samsung |
South Korea |
130,000 dmt/year |
H2 2013 |
Several plants |
China |
500,000 dmt/year |
During 2013 |
Aditya Birla Chemicals |
India |
180,000-240,000 dmt |
Q1 2013 |
($1 = €0.77)
Global News + ICIS Chemical Business (ICB)
See the full picture, with unlimited access to ICIS chemicals news across all markets and regions, plus ICB, the industry-leading magazine for the chemicals industry.
Contact us
Partnering with ICIS unlocks a vision of a future you can trust and achieve. We leverage our unrivalled network of industry experts to deliver a comprehensive market view based on independent and reliable data, insight and analytics.
Contact us to learn how we can support you as you transact today and plan for tomorrow.
READ MORE
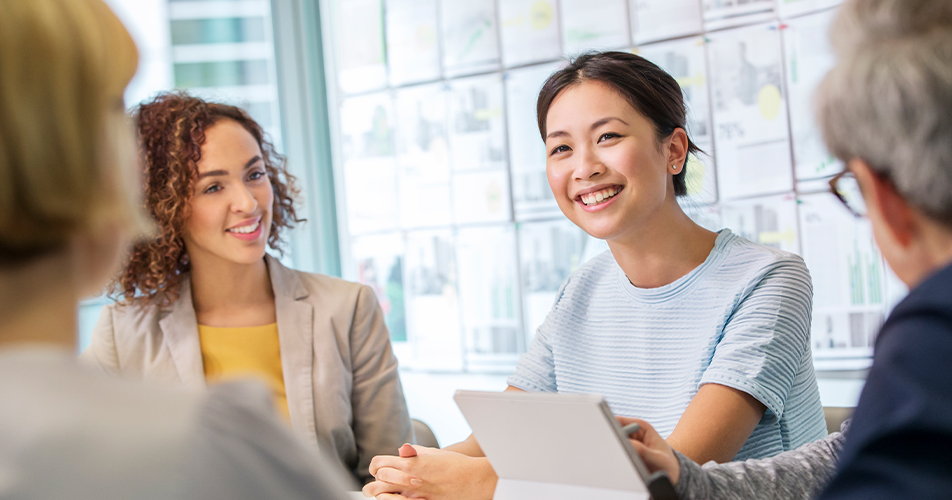