INSIGHT: Pandemic to accelerate shift from global to local supply chains
Will Beacham
19-Aug-2020
BARCELONA (ICIS)–The shift from global to more local supply chains was already under way before the coronavirus pandemic kicked in, exposing more vulnerabilities.
From 2018 the US-China trade war politicised movement of goods, with tariff and non-tariff barriers causing companies to explore new markets and sources of raw materials.
When the pandemic began, supply chains relying on components first from Hubei and then the rest of China were the first to be impacted. As lockdowns spread across first Asia, then Europe and the US, the chemical industry experienced a supply and demand shock unlike anything in living memory.
Ships waited for weeks at ports in Asia for enough containers to load to make it worth their while setting sail for Europe. Then further delays piled on as ships’ crews were forced to quarantine on arrival at destination ports.
Governments began to take notice when it became apparent that stockpiles of essential pharmaceuticals and personal protective equipment were running low. Supplies of active pharmaceutical ingredients (APIs) were cut as India and China – which dominate the market – imposed export restrictions or suffered interruptions to their own supply chains.
Underlying all this pressure on supply chains is another driver for change – the sustainability agenda, and recycling. Local supply chains fit perfectly with the circular concept of chemical waste, particularly polymers, being recycled and reprocessed within cities or regions.
As the global economy stabilises, chemical companies, their customers and suppliers, will be thinking about the pros and cons of diversifying or reshoring supply chains to protect against future shocks.
Two studies released in August highlight the strains on supply chains and look at how they could change in the next few years.
US-headquartered legal group Baker McKenzie’s new report says global companies which are reliant on Asia-Pacific supply chains must think carefully about the pros and cons of reducing exposure to, say, the market in China. Its research interviews show that there is strong sentiment to continue investing in China, despite the US-China trade war.
Certainly for many global chemical companies, a continuing footprint in China does make sense as it is the world’s largest chemicals market.
Increasing tension between the US and China may lead to the creation of a polarised global economy, with tough tariff and non-tariff barriers separating the two. One region would comprise China and its Belt and Road allies in emerging economies. The US and its allies would occupy the other region.
This scenario would give another reason to maintain chemical production within the China region as it has access to many of the world’s remaining emerging economies.
HARNESSING
DIGITISATION
Digitisation may be
able to reduce some of the risks, bottlenecks
and under-performance in complex supply chains.
Baker McKenzie points out that pre-emptive risk
management and geospatial analytics can now
play a greater role.
“Being able to fully map their supply chain to understand the geographic location of suppliers and feed the maps with alternative data (such as flood maps) can help companies to have in-built defences against large shocks to their supplier ecosystems.”
Companies may also look to identify where they are reliant on a single supplier in a high-risk location (such as a flood-prone industrial park) or on a cluster of suppliers all in the same concentrated area.
Other technologies such as the use of 3D printers will continue to be a driver for supply chain shifts.
Barker McKenzie points out that re-creating supply of APIs at a local level may be hindered by a lack of chemical feedstocks for production.
The report says buyers who want to make supply chains more robust must focus on regionalisation, diversification and digitisation.
- Regionalisation – need to balance the need to bring manufacturing “back home” against higher production costs
- Diversification – avoid the use of single source suppliers, build up alternative sources to avoid interruptions to supply
- Digitisation – helps companies react quickly to market, environmental, sustainability challenges. Secure new sources of supply, scale up new processes
Consultancy McKinsey’s new report analyses the impact of more shocks to supply chains from natural disasters, geopolitical events, the fragility of just-in-time deliveries and use of single suppliers.
Trade in manufactured goods soared in the 1990s and early 2000s, propelled by China’s entry into the World Trade Organization and the search by multinational companies for lower-cost inputs and wages.
CHEMICAL COMPANIES FACE
LOSSES
It projects that chemical
companies can now expect to lose 35% of one
year’s operating profit every decade from
supply chain disruptions. These include
climate change, macroeconomic/financial crises,
trade disputes, pandemics, cyber attacks,
terrorism and supplier bankruptcy.
Bearing in mind the increasing risks to global supply chains it estimates that 16-26% of global goods exports, worth $2.9-4.6tr, could conceivably move to new countries over the next five years if companies restructure their supplier networks.
In McKinsey’s analysis, labour-intensive value chains such as furniture, textiles and apparel are more likely to shift.
This is already under way with higher labour costs in China driving clothing manufacture to lower cost countries such as Bangladesh. In 2005, China exported 71% of its finished clothing goods. This fell to 29% in 2018 as companies refocused on domestic demand.
McKinsey estimates 36-57% of clothing supply chains could move, some to the EU and US, but most to southeast Asian countries.
For the global pharmaceutical value chain, 38-60% could shift geographically. But this is driven less by economics than governments which want to re-establish domestic manufacture. McKinsey points out that China currently accounts for more than 60% of global exports of antibiotics, sedatives, ibuprofen, and acetaminophen.
The important automotive sector is already very regionalised, says the report, and with countries doing their best to retain domestic manufacturing, only 15-20% of auto exports has the potential to move, driven by non-economic factors.
McKinsey’s May 2020 survey of 605 business executives highlights the actions leaders are taking to boost resilience in their supply chains.
They also highlight supply chain vulnerabilities identified by respondents from the chemical sector and other major markets.
Insight article by Will
Beacham
Thumbnail picture: workers unload
a cargo plane in the US. Source: Erik S
Lesser/EPA-EFE/Shutterstock
Global News + ICIS Chemical Business (ICB)
See the full picture, with unlimited access to ICIS chemicals news across all markets and regions, plus ICB, the industry-leading magazine for the chemicals industry.
Contact us
Partnering with ICIS unlocks a vision of a future you can trust and achieve. We leverage our unrivalled network of industry experts to deliver a comprehensive market view based on independent and reliable data, insight and analytics.
Contact us to learn how we can support you as you transact today and plan for tomorrow.
READ MORE
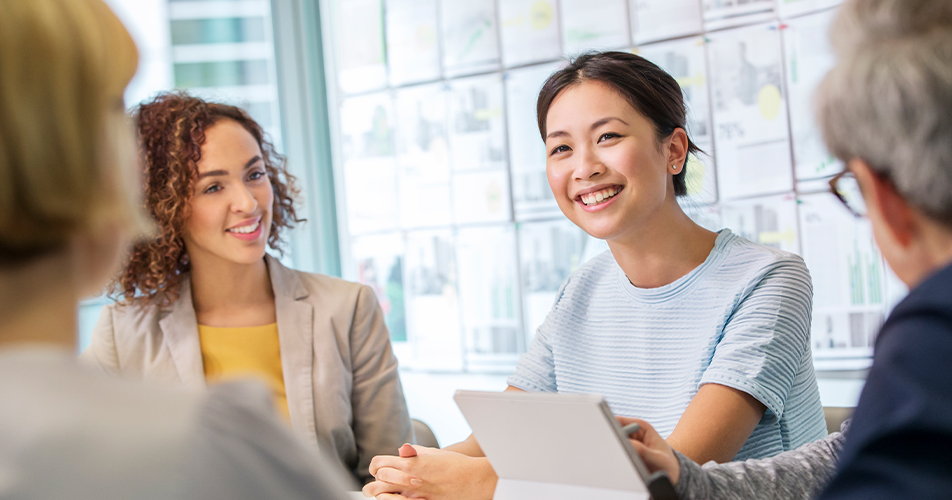