INSIGHT: Chemical recycling as a method to tackle the circularity of flexibles
Joshua Dill
09-Feb-2024
HOUSTON (ICIS)–Film plastics, more commonly known as flexibles, are a recurring obstacle in the path of recycling as they are notoriously hard to deal with via traditional recycling methods. Several key aspects make flexibles challenging for recycling:
- They are soft and bendable, leading to easy clogging of recycling machines
- Their relatively lightweight nature makes them difficult to handle on sorting lines
- They are not typically accepted in curbside recycling programs
Flexibles are commonly comprised of two main polymer types: low-density polyethylene (LDPE) and linear low-density polyethylene (LLDPE). They are heavily utilized in the packaging industry, for both food and non-food packaging—a trend that shows no sign of slowing down.
The relatively low quantity of LDPE and LLDPE flexibles being mechanically recycled, especially when compared to their rigid high-density polyethylene (HDPE) counterpart, alludes to the challenges that many mechanical recyclers encounter in recycling these polymers. One useful metric to quantify this difference is to compare the mechanical recycling penetration percentages for LDPE+LLDPE and HDPE.
The mechanical recycling penetration of LDPE+LLDPE for 2023 can be found by comparing the total mechanical recycling output of LDPE+LLDPE in 2023 to the amount of LDPE+LLDPE that was consumed in the same year. The graph below, extracted from the ICIS Supply and Demand Database and Recycling Supply Tracker – Mechanical, shows the mechanical recycling penetration for both LDPE+LLDPE in North America, as well as HDPE for comparison.
Sources: ICIS
Supply and Demand Database and Mechanical
Recycling Supply Tracker, January
2024
Mechanical Penetration of Polymer for 2023
= (Mechanical Recycling Output of Polymer in
2023)/(Consumption of Polymer in 2023)
Despite similar consumption volumes for 2023, significantly more HDPE is making its way back into the market via mechanical recycling than LDPE+LLDPE. One primary reason for this difference is the inherent characteristics of flexibles. They are lightweight and pliable, making them excellent choices for packaging. However, these same qualities are obstacles to traditional recycling processes.
The recycling journey begins with collection, a crucial stage where the disposability and public perceptions of plastic films play a pivotal role. Many consumers, influenced by the nature of these films, tend to discard them in the trash, viewing them as potentially contaminated or unaware of their recyclability. Consequently, these items seldom find their way to recycling facilities.
A significant challenge emerges for those who make an effort to recycle these packaging materials: they are often not accepted for curbside recycling in numerous states in the US. Instead, recycling them frequently requires a separate collection process and participation via an in-store recycling program.
All these additional steps for consumers—including separating materials, identifying drop-off locations, and investing time in transportation—add another layer of complexity to the recycling process for flexibles.
Flexibles also pose a challenge at the material recovery facility (MRF) level, disrupting much of the sorting machinery. Consequently, flexibles that do make their way to MRFs are susceptible to improper sorting and potential diversion into waste streams.
To achieve a high-quality pellet output, mechanical recyclers require a high quality of feedstock. This means sorting capacities to deliver bales with low contamination levels, which remains difficult to achieve consistently.
The reality is that mechanical recyclers must further sort to extract the useable volumes required. This is more challenging to achieve at the required volume and quality for flexibles, particularly in a cost-effective way.
In such situations, chemical recycling emerges as a viable complementary technology. Chemical recycling primarily involves breaking down polymers into their fundamental components. Polyethylene polymers, including HDPE, LDPE, and LLDPE, share the same base parts, enabling them to be processed together as mixed plastic bales for chemical recycling. This option, unavailable in mechanical recycling, alleviates the pressure of sorting waste into individual polymer types.
Nevertheless, it is crucial to acknowledge that the degree of sorting still impacts chemical recycling outcomes. Even with chemical recycling, certain contaminants will negatively impact the process and should be removed. Generally, a better-sorted stream yields superior results, regardless of the recycling method.
Techniques like pyrolysis and gasification further expand the possibilities for the recycling of polyethylene polymers, as they are better equipped to handle these particular feedstocks. According to ICIS Recycling Supply Tracker – Chemical, operating pyrolysis plants in the US account for nearly 28% of the total chemical recycling operating capacity available in 2023. However, that number is anticipated to increase to over 60% of the total chemical recycling operating capacity in 2028 based on announced projects.
Sources: ICIS
Chemical Recycling Supply Tracker, January
2024
Another inevitable challenge tied to mechanical recycling is the limited ability to recycle continuously. After a certain number of cycles, plastics undergo degradation in their physical qualities. Chemical recycling, by breaking down plastics to their base form, provides an alternative route for plastics that can no longer undergo mechanical recycling.
Although chemical recycling offers relief in situations where mechanical recycling is limited, it is still a relatively new process, especially when compared to the more established mechanical recycling methods. As a result, it will take time to establish feedstock streams and achieve consistent and maintainable yields.
The constant shifts in the legal landscape do not help to clarify the situation surrounding chemical recycling. In the US there is no consensus on whether chemical recycling should be classified as a form of recycling. Presently, 24 states have legislation acknowledging chemical recycling as an acceptable method.
As another result of the novelty of chemical recycling, there are limited impartial studies that have been done surrounding its environmental impact. Even the name ‘chemical recycling’ signifies to some that the process is inherently bad for the environment, a claim that is not substantiated.
There are many different processes that fit under the umbrella of chemical recycling, each requiring thorough and unbiased analyses to be conducted as the technologies mature.
While mechanical and chemical recycling both undoubtedly have their drawbacks, one thing is certain: there is a problem of plastic waste that needs to be addressed.
It will take the combined efforts of mechanical recycling, chemical recycling, and many other methods in unison to combat this crisis.
Insight by Joshua Dill
Global News + ICIS Chemical Business (ICB)
See the full picture, with unlimited access to ICIS chemicals news across all markets and regions, plus ICB, the industry-leading magazine for the chemicals industry.
Contact us
Partnering with ICIS unlocks a vision of a future you can trust and achieve. We leverage our unrivalled network of industry experts to deliver a comprehensive market view based on independent and reliable data, insight and analytics.
Contact us to learn how we can support you as you transact today and plan for tomorrow.
READ MORE
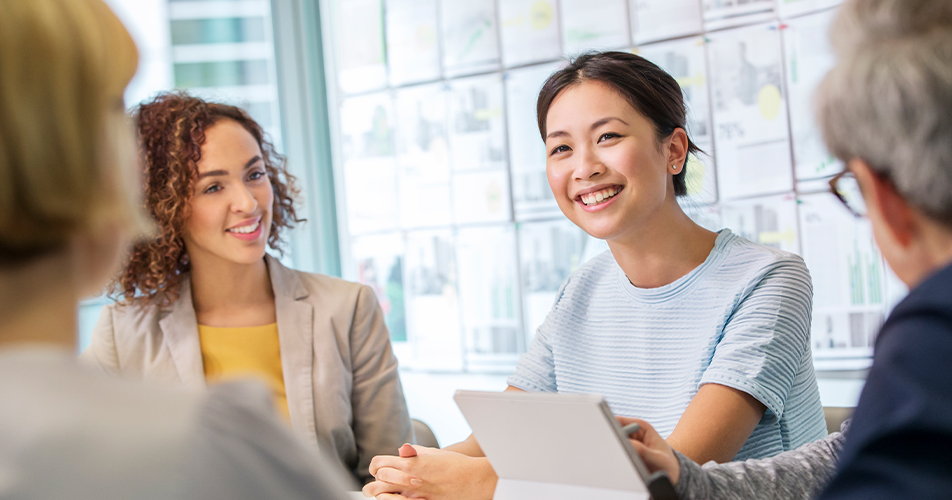