New regulations drive plastic additives research
Sean Milmo
18-Jun-2009
Restrictions on the use of many traditional plastics additives are challenging producers to innovate
PLASTIC ADDITIVES manufacturers are under increasing pressure to supply chemicals that are safer and more environmentally friendly than existing products. Yet they must develop these new additives at a time when recession is dramatically reducing demand in most of their markets.
Bans and restrictions on a range of plastic additives have been introduced in recent years in Europe and North America, because of their danger to human health and the environment. Developing nations are adapting to the regulations out of economic necessity.
The EU has been the most active in imposing strict curbs on long-established flame retardants, plasticizers, colorants and other additives. These are being controlled through legislation such as Restriction on Hazardous Substances (RoHS) in electrical and electronic equipment,the Waste Electrical and Electronic Equipment (WEEE) directive and the European chemical registration legislation Reach.
At the end of last year, the European Commission introduced RoHS2 , which extended the legislation’s scope to medical devices and monitoring equipment and restricted more substances. The Commission has also decided that under Reach, three plasticizers, one flame retardant and a pigment used in plastics will have to go through an authorization process if they are to stay on the market.
In the US, controls on the use of phthalates in toys and other children’s products were introduced earlier this year through the Consumer Products Safety Improvement Act (CPSIA).
Globalization is forcing emerging economies such as China, with its heavy reliance on export markets in developed countries, to comply with standards in Europe and North America, and even to introduce their own.
In fact, China’s own RoHS legislation, called Management Methods for Controlling Pollution from Electronic Information Products, is considered, in some respects, to be stricter than the original EU version.
Original equipment manufacturers (OEMs) supplying the global market for electrical and electronic products are striving to keep ahead of legislation by introducing their own standards for plastic additives, as well as the polymers themselves.
US-based consumer electronics maker Apple, for example, claims that the “greatest challenge” facing the electronics industry is the presence in its products of substances and materials such as arsenic, mercury, brominated flame retardants (BFRs), phthalates and polyvinyl chloride (PVC). “Apple is not waiting for legislation to ban these substances,” the company said in a policy statement.
Other OEMs have similar objectives. US-based computer maker Hewlett-Packard has drawn up guidelines for its design teams and suppliers that prohibit or restrict the use of certain substances.
“A lot of R&D [research and development] money is now being spent on the development of safer alternatives to certain additives, because the rewards could be enormous,” says one German-based consultant. “A company introducing an alternative which is safer and performs well will inevitably gain a large share of the market.”
Flame retardants
Flame retardants are among the most common and varied of
plastic additives, with hundreds of different substances on
the market for preventing or inhibiting the spread of fire in
polymers. Much of their demand is driven by fire safety
legislation covering consumer products.
Of the three main types – halogen, phosphorus and mineral – halogenated (brominated or chlorinated) flame retardants have raised by far the most concern. RoHS, which came into effect in the EU in 2006, banned a number of BFRs, the production of which in the developed world had already been discontinued. Last year, the RoHS exemption of decabromodiphenyl ether, one of the most common flame retardants, was withdrawn.
Hexabromocyclododecane has become the first brominated flame retardant to be listed as requiring authorization for marketing in the EU under Reach. It is used in polystyrene (PS) materials for building insulation and packaging.
Apple had aimed to remove BFRs from all new product designs by the end of last year. Hewlett-Packard plans to eliminate them from all new computing products, but, the company stresses, only “as technologically feasible alternatives become readily available that will not compromise product performance or quality.”
BFRs are popular because of their low cost and efficiency. The amounts required in a polyolefin or polyamide product are half to two-thirds less than those for flame-retardant minerals such as aluminum trihydrate and antimony.
The closest substitutes in performance are phosphorus-based retardants, which intumesce (or swell) as a carbonized foam to stop the spread of flame. Germany-based LANXESS has introduced phosphorus compounds that create an intumescent barrier for flame retardation in polyurethane (PU) insulation materials.
Switzerland-based Clariant’s Exolit range of phosphorus flame retardants gives fire protection to polyamides and polyester, particularly in fiberglass-reinforced products and in circuit boards.
Flame retardants based on emerging technologies have the problem of a lack of test data, which can considerably delay their introduction into the market. Trulstech, a group of technology companies in the Europe, US and Australia, has developed an intumescence system using only water, citrates and acetate.
“The product is being tested at the moment by several companies but some of the tests may have to take place over several years,” says Frederick Westein, managing director of Sweden-based Deflamo, which has the marketing rights to the technology in much of Western Europe. “Nonetheless, the interest is so strong that we are expecting to take a 10% share of our market by 2015.”
Plasticizers
In
volume terms, plasticizers have by far the biggest share of
many plastic additives markets, particularly in the emerging
economies, where there is a high consumption of PVC, the main
driver behind demand for plasticizers. In China and India,
plasticizers make up around two-thirds of demand for plastic
additives, according to Townsend
Solutions, a US-based polymer consultancy.
Most plasticizers are phthalates, consisting of compounds of phthalic anhydride and various alcohols, whose safety has been raising concerns among regulators and OEMs.
Three phthalates – benzyl butyl phthalate (BBP), dibutyl phthalate (DBP), and di-2-ethylhexyl phthalate (DEHP) – have been allocated for priority review under RoHS by the European Commission and listed for authorization under Reach.
Both DEHP and DBP are used in PVC and other polymers for medical devices and packaging, as well as PVC flooring and roofing.
Among OEMs, Hewlett-Packard is aiming to remove DEHP, DBP and BBP from its products by next year. Apple lists phthalates among substances being removed from its products, including DEHP, DBP and BBP as well as di-isononyl phthalate.
The strong demand for phthalate alternatives has been demonstrated by the rapid growth over the past few years of German producer BASF’s nonphthalate plasticizer Hexamoll DINCH. Its production capacity at Ludwigshafen, Germany, was quadrupled to 100,000 tonnes/year in 2007. The company continues to supply 13 phthalate plasticizers.
In a recent study of four nonphthalate plasticizers comprising Hexamoll, diethylhexylterephthalate, alkylsulfonic phenyl ester, acetyltributyl citrate and an acetylated castor oil derivative, the German research organization TUV Rheinland found that the BASF product was the most eco-efficient.
US-based specialized polymer producer PolyOne last year licensed a series of technologies from the US-based nonprofit science firm Battelle for bio-based plasticizers. It has also agreed to collaborate with US-based agrosciences firm Archer Daniels Midland on the development of bio-based plasticizers.
Pigments
Safety
concerns about the insolubility of substances in their
pigments have forced colorant producers to reformulate
products used in plastics, particularly in Europe. Europe’s
WEEE directive, for example, has led to the elimination of
heavy metals in some plastics pigments for electronics.
Colorant makers are also worried that under Reach, some pigments may be classified as persistent, bioaccumulative and toxic, or very persistent and very bioaccumulative. This would mean they would have to be authorized or replaced by safer alternatives.
Producers have been developing clean pigments, while also meeting the aesthetic demands of end-users. “Developments in colorant are designed to meet both the demand for greater choice in color and design and to be suitable for purity-demanding applications such as toys, cosmetics and food packaging,” says Nicola Lelli, global head of marketing, industry platform plastics, at Ciba, now part of BASF.
Over the next few years, the pigment content of plastics could decrease in response to changes in consumer preferences influenced by economic conditions. Cristina Carrara, designer at Clariant ColorWorks Europe in Italy, believes that there will be a need for “soft and understated” colors. “The bright primary colors that were popular over the last few years are disappearing,” she says, while nature and ecology will have a greater influence.
This trend has been exemplified by Clariant’s promotion of a masterbatch range for polylactic acid biopolymers comprising natural pigments derived from plants.
At the same time, pigment producers are not only expanding the source of raw materials for plastic colorants, but also developing pigments and dyes for plastics that have previously been considered difficult to color.
Plummeting sales could put a crimp in R&D budgets, however. Many of the major additives producers reported losses in the first quarter of this year, after sharp falls in revenue. US producer Chemtura recorded a 43% drop in sales.
Townsend reckons that the average global growth rate in volume demand for plastic additives in 2007-2012, which it previously forecast to be 4.6%, could now decrease to about 3%. Additive producers will have a challenging time innovating in such an environment.
Global News + ICIS Chemical Business (ICB)
See the full picture, with unlimited access to ICIS chemicals news across all markets and regions, plus ICB, the industry-leading magazine for the chemicals industry.
Contact us
Partnering with ICIS unlocks a vision of a future you can trust and achieve. We leverage our unrivalled network of industry experts to deliver a comprehensive market view based on independent and reliable data, insight and analytics.
Contact us to learn how we can support you as you transact today and plan for tomorrow.
READ MORE
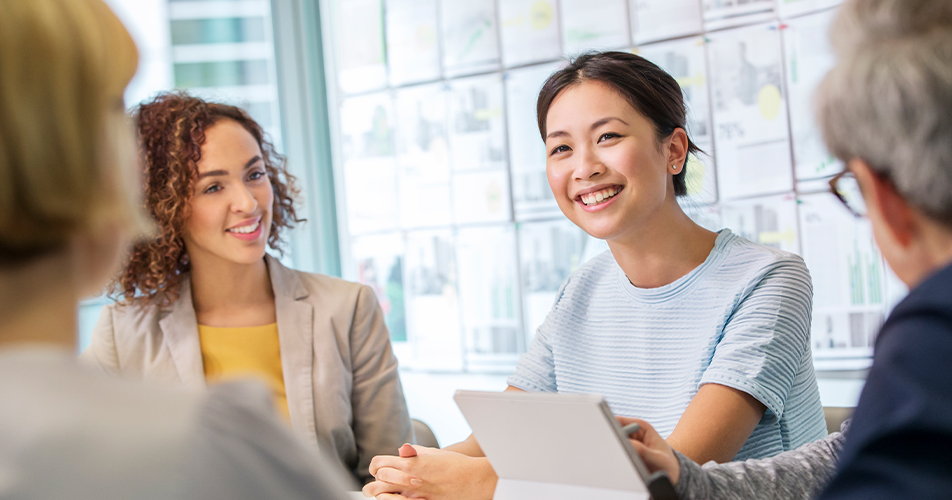