Eastman rolling out two large-scale chems-recycling projects
Al Greenwood
26-Apr-2019
Eastman plans to roll out two large-scale chemical recycling projects, with one starting as soon as this year.
Companies are eager to develop chemical recycling technology, as they face increasing backlash against plastic waste. Nearly all of the plastic that is recycled currently is done mechanically, in which it is cleaned, processed, re-melted and mixed with additives and virgin resin.
Although mechanical recycling has been used for decades, it has significant limitations, Eastman said. It requires very pure feedstocks, which have limited its use primarily to bottle-grade polyethylene terephthalate (PET) and high-density polyethylene (HDPE).
This means that the majority of plastics waste either ends up in landfills or incinerators, Eastman said. Additionally, mechanically recycled plastic can be used only a limited number of times before its properties degrade and the material has to be discarded.
Chemical recycling avoids this, since it breaks down plastic back into its monomers. Some still consider it an infant technology that needs several more years of development before becoming mainstream. Companies such as Eastman are showing that chemical recycling could become adopted sooner than expected.
One of Eastman’s processes, Carbon Renewal Technology, allows the company to use plastic waste alongside coal in its gasification unit in Kingsport, Tennessee, to produce synthesis gas (syngas).
Syngas contains carbon monoxide (CO) and hydrogen gas, which Eastman uses to make acetic acid and other acetyls. These, in turn, are used in the company’s Advanced Materials, Additives and Functional Products, and Fibers segments.
Because Eastman is modifying an existing plant, it should start using the technology later this year.
METHANOL
The company’s Advanced Circular Recycling Technology will use methanol to break down waste polyethylene terephthalate (PET) into monoethylene glycol (MEG) and dimethyl terephthalate (DMT). Eastman will then use most of the output of the plant to produce specialty co-polyesters. The goal is to operate a full-scale plant within 24-36 months, Eastman said.
Eastman can have such a rapid timeline for a commercial-scale plant because it is using proven technology developed nearly half a century ago. For years, Eastman used the process technology to recycle used photographic film back when it was still part of Kodak. Eastman is developing commercial-scale projects in a field that the industry treats as a young technology, with some executives saying that chemical recycling could be 5-10 years away from becoming mainstream.
Many chemical-recycling technologies are focusing on pyrolysis, which would use heat in an oxygen-starved environment to break up plastic waste into raw materials that could later be used to make chemicals.
Eastman’s two technologies are foregoing pyrolysis entirely. Its Carbon Renewal Technology relies on gasification to convert plastic film and mixed plastic waste into syngas.
Eastman has run trials on the technology and the resulting products made from the gasification process are indistinguishable from virgin material, said Tim Dell, vice president of corporate innovation for Eastman.
RECOVERY OF CHALLENGING WASTE
Eastman did not say how much plastic it could consume in its gasification plant. However, it could very well be the first company to use such a process to produce syngas for chemical production on a large scale.
The plastic waste that Eastman is targeting is the very type of trash that US recycling plants are ill-equipped to handle.
These plants were built to handle clean, higher purity feedstock from plastic bottles, while the plastics industry needs solutions for the more challenging streams such as packaging film and other food containers and non-bottle rigid plastic, Eastman said. Carbon Renewal Technology provides a solution for most mixed plastic waste streams.
Outside of landfills and incineration, these plastics have very few good options for recovery, said Ron Sheppard, director, corporate innovation at Eastman. The other technology, Advanced Circular Recycling Technology, was developed back in the 1970s to recover silver and recycle polyester from used photographic film, Sheppard said.
Eastman actually built a commercial-scale plant using the process technology and continued running it for several years, Sheppard said. Eastman used the chemicals to produce PET for packaging, which it marketed as having 25% recycled content.
“We had experience running the materials, understanding how to purify them and what’s required to make good products out of those materials,” he said.
Early this decade, Eastman considered building a new plant using an updated version of its methanolysis technology, Sheppard said. At the time, economic conditions and market demand were not sufficient to justify building the plant. That changed sharply in the past couple of years, with public sentiment swinging sharply in favour of recycling plastics.
Eastman re-assembled the team and revived the methanolysis project, Sheppard said.
For both the methanolysis and gasification process technologies, one of the biggest challenges is collecting enough of the feedstock to feed a commercial-scale plant. This goes beyond logistics, Dell said.
The plastic waste needs to be collected, gathered up and processed into a form that can be used as feedstock in Eastman’s plants.
“That involves building a supply chain, a value chain, that for the most part doesn’t exist today,” Dell said.
PARTNERSHIPS
Eastman wants to solve this problem by developing partnerships with waste-management companies, and other businesses, he said. Eastman is also working with potential customers so it can find an outlet for the co-polyesters it plans to produce from plastic waste.
Companies that make consumer products are eager to replace materials with more recycled content. These companies are also facing consumer and regulatory backlash against plastics. Other companies may set independent goals for recycled content as a way strengthen their brands. Some are willing to pay a so-called green premium.
“The market conditions have changed pretty dramatically in the last five to eight years,” Dell said.
Companies with valuable brands are making a lot of commitments that will drastically change the profile of the products that they make – from making them easier to recycle to being derived from increasing amounts of recycled material, he said. “There simply isn’t enough recycled material available today from traditional routes in order to meet these commitments.”
Click here to see regulatory targets and a list of chemical and mechanical recyclers on the ICIS Circular Economy topic page.
Global News + ICIS Chemical Business (ICB)
See the full picture, with unlimited access to ICIS chemicals news across all markets and regions, plus ICB, the industry-leading magazine for the chemicals industry.
Contact us
Partnering with ICIS unlocks a vision of a future you can trust and achieve. We leverage our unrivalled network of industry experts to deliver a comprehensive market view based on independent and reliable data, insight and analytics.
Contact us to learn how we can support you as you transact today and plan for tomorrow.
READ MORE
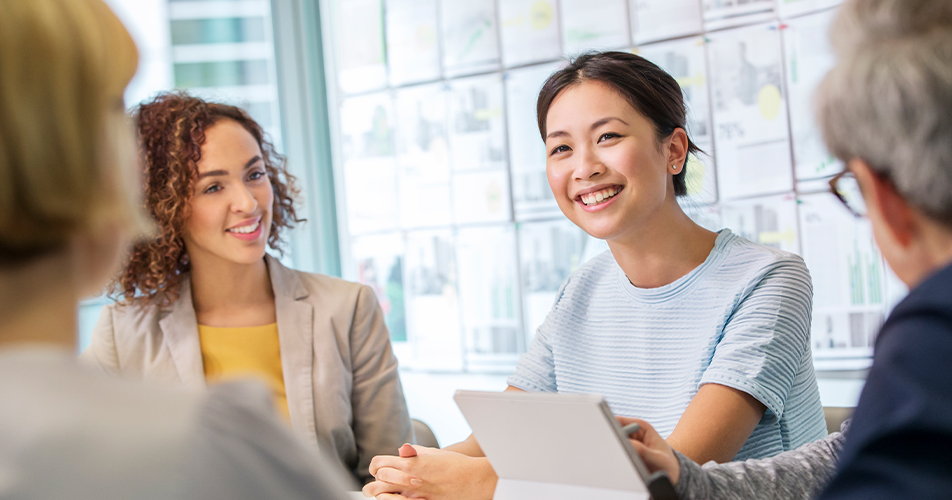