INSIGHT: US Origin seeks to make PX from biomass
Al Greenwood
18-Mar-2021
HOUSTON (ICIS)–Origin Materials is developing a process to convert biomass into paraxylene (PX) that, if successful, could achieve the elusive goal of converting the renewable feedstock into chemicals.
Origin’s PX is not only renewable, it is carbon negative, which would help companies offset their greenhouse gase emissions and meet their net-zero carbon goals.
Since PX is used to make polyethylene terephthalate (PET), a cost-competitive, carbon-negative material could find a ready market among food and beverage companies with valuable brands.
A big question will revolve around the product mix of an at-scale plant. Origin’s process makes hydrothermal carbon (HTC) in addition to 5-chloromethyl-furfural (CMF), the intermediate it uses to make PX. It makes smaller amounts of furfural and levulinic acid.
Still, Origin has attracted the interest of Artius Acquisition Inc, a special purpose acquisition company (SPAC) that is conducting a reverse merger that will take Origin public.
So far, Origin has lined up about $1bn worth of signed contracts and another $400m of deals under negotiation.
It expects to start up its demonstration plant in 2023. An at-scale plant could start operations in 2025.
HOW THE TECH WORKS
Origin
relies on an homogenous catalyst mix to convert
woody biomass into mostly CMF and hydrothermal
carbon, with smaller amounts of furfural and
levulinic acid. The yields of these products
depend on the composition of the biomass.
Biomass is made up of cellulose, hemicellulose and lignin, and their proportions can alter Origin’s product slate.
Origin wants biomass with as much cellulose as possible, since this maximises CMF yields, said John Bissell, co-CEO of Origin. He made his comments in an interview with ICIS.
Origin’s process converts glucose and other C6 sugars into CMF at high double-digit yields, he said.
The C5 sugars in hemicellulose are converted into furfural at yields of about 90%.
The lignin as well as some of the sugars are converted into hydrothermal carbon (HTC). This is made up of macro-fragments of lignin that are coated with polymers derived from furfural and CMF. Bissell compares the material to a lignin-supported furan Bakelite.
The process also produces relatively small amounts of levulinic acid.
Very little of the carbon of the biomass is converted into carbon dioxide (CO2) or other waste, Bissell said. “We basically don’t lose carbon in the process.”
Origin has not disclosed the yields of CMF in relation hydrothermal carbon and the other by-products. It has said that the production of furfural and levulinic acid is relatively small when compared with that for CMF and hydrothermal carbon.
Deloitte conducted a study that assesses how much of the biomass’s carbon ends up in each of the four products. The study, though, does not take into account the weight of the other elements in the products, such as the chlorine in CMF.
CARBON-NEGATIVE PET
BOTTLE
Companies have
long sought out a way to make renewable PX.
PX is used to make purified terepthlatic acid
(PTA), which is combined with monoethylene
glycol (MEG) to make PET.
Companies can already make renewable MEG by dehydrating ethanol to make ethylene.
Not only could Origin provide a renewable route for the second PET feedstock, it would do so in a way that removes carbon from the atmosphere. Each kilogram of CMF has the effect of removing 1.21 kg of CO2 from the atmosphere, according to Deloitte’s life-cycle assessment.
Moreover, Bissell said Origin’s process is competitive against petroleum-based PX with oil prices well below $50/bbl.
Low-cost CMF could be used to make other products. One that stands out is polyethylene furanoate (PEF).
PEF is a polyester with similar properties to PET. However, it has a higher gas barrier against oxygen, CO2 and water vapour, eliminating the need for most of the multilayers used in PET bottles, Bissell said.
PEF can degrade in a way similar to another renewable polymer, polylactic acid (PLA).
Until now, cost has prevented the widespread adoption of PEF. Bissell said Origin’s process could lower PEF’s costs to levels closer to those for PET.
Other uses for CMF are as a feedstock to make adipic acid, one of the monomers used to make nylon 6,6. Another is vinyl toluene, Bissell said. This has properties similar to styrene but without as many of the toxicity concerns.
Origin’s other main product, hydrothermal carbon, can be burned for energy or further processed into other materials, Bissell said.
One area of interest is carbon black, since Origin’s hydrothermal carbon shares a similar nanostructure, Bissell said. Origin’s material would lack the polyaromatic hydrocarbons of petroleum-based material, and the company can make it at a lower cost.
Like Origin’s CMF, its hydrothermal carbon is carbon negative. Each kilogram of hydrothermal carbon removes the equivalent of 1.67kg of CO2 from the atmosphere, according to the Deloitte assessment.
CHALLENGES OF CONVERTING
BIOMASS
Biomass has proven
difficult to convert into feedstock or fuels
because the material is so heterogenous, as it
is composed of varying amounts of cellulose,
hemicellulose and lignin.
Fermenters focused on using the cellulose portion of biomass, since they can break down the material into sugars that their microbes can convert into fuel and chemicals. The problem was finding a profitable use for lignin. Fermenters resorted to burning it for fuel.
Other companies resorted to gasifying biomass to produce synthesis gas (syngas). INEOS Bio and Rentech both pursued gasification only to abandon their projects.
Another company, KiOR, based its technology on a modified fluid catalytic cracking (FCC) unit. The project proved to be a failure, and KiOR went bankrupt.
Anellotech had been converting biomass into aromatics at a pilot plant in Texas using its Bio-TCat process. In it, the prepared biomass is heated rapidly in a fluidised catalytic bed reactor, producing aromatics along with carbon monoxide (CO), carbon dioxide (CO2) and water.
Anellotech is now focusing on using waste plastic as a feedstock.
Insight by Al Greenwood
Thumbnail photo shows bottles made of PET. Source: imageBROKER/REX/Shutterstock
Global News + ICIS Chemical Business (ICB)
See the full picture, with unlimited access to ICIS chemicals news across all markets and regions, plus ICB, the industry-leading magazine for the chemicals industry.
Contact us
Partnering with ICIS unlocks a vision of a future you can trust and achieve. We leverage our unrivalled network of industry experts to deliver a comprehensive market view based on independent and reliable data, insight and analytics.
Contact us to learn how we can support you as you transact today and plan for tomorrow.
READ MORE
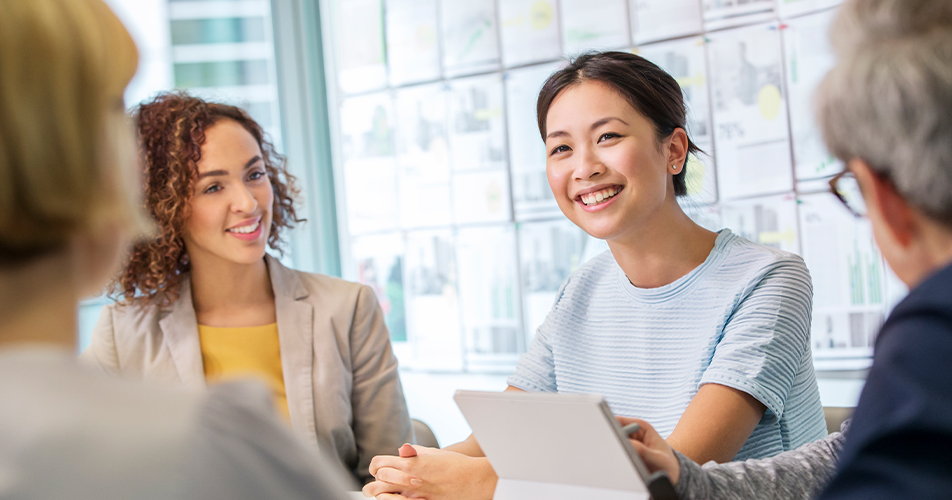