Huntsman Textile Effects restructures to compete with a changing market
Stefan Baumgarten
27-Aug-2008
A massive restructuring aligns Huntsman Textile Effects with the needs of a competitive and changing market
THE TEXTILE chemical business, one of the chemical industry’s oldest sectors, is undergoing fundamental changes.
Demand and production continue to follow the apparel market toward the emerging economies of China, India and Vietnam. Raw material and energy costs are hitting record highs, and the global economic outlook is uncertain.
Among the major Western players adapting to the fluid situation is US specialty chemical company Huntsman, which became a leader in the sector through its acquisition of Switzerland-based Ciba’s textile chemical business two years ago. Last year, the company further bulked up by acquiring US-based DuPont’s global fluorochemicals business for the nonwovens industry.
In the combined dye and textile chemical market, Huntsman claims 9% of a total market volume of $11bn (€7.5bn). Within the markets it serves, the company sees its share at around 13-14%.
Today, Huntsman Textile Effects, which has its headquarters in Switzerland, is a $1bn/year business that accounts for 10% of its parent’s overall revenues. Earnings before interest, tax, depreciation and amortization (EBITDA) are below Huntsman’s overall average EBITDA, but Paul Hulme, division president of materials and effects, is unfazed.
“We acquired this business because of its growth and turnaround potential,” he says.
“We are confident that our restructuring and the reorganization of the business positions us well to compete successfully in the textile chemicals market.”
Hulme elaborates on the business history. “We are the market leader in technology innovations and we have a long tradition in textiles,” he says. “Over the long term, we believe our business has a bright future.”
As part of a five-year plan for the business, Huntsman expects revenue growth above the global GDP rate, and EBITDA in line with Huntsman’s other businesses, Hulme says.
In the 2008 second quarter, which ended June 30, Huntsman Textile Effects’ revenues were essentially flat year on year, while volumes dropped by 14% as a result of slower demand in Europe and the Americas.
ECONOMIC IMPACT
“Because the textiles market tends to be a leading indicator of the global economy, like our competitors, Huntsman Textile Effects business has been affected by the global economic slowdown,” says Hulme.
“We believe that the environment for the business in 2008 will continue to be demanding, with a slight improvement in 2009.”
As with any organic chemicals business, Huntsman’s textile chemicals are affected by the rising costs of raw materials and energy.
“Overall raw material costs are at an all-time high,” says Hulme.
The company is countering this by making substantial price increases and cost-savings measures.
“This is an issue for the whole value chain, from the chemical manufacturers, all the way to the consumer,” says Hulme.
Recent price increases to offset the unprecedented leaps in raw material costs are generally being accepted by customers as a necessary response, he stresses.
Unfavorable exchange rates can also occasionally create a significant burden to Huntsman’s textiles business, just as is the case with its competitors, Hulme says.
“We believe these are all short-term challenges to our business and the textile chemicals industry generally,” he says. “Importantly, the current challenges facing our Textile Effects business do not threaten the long-term viability of this business. The combination of our price increases, reduction of costs where appropriate, and the restructuring and reorganization of our Textile Effects business position us well to compete effectively over the long term in this market.”
RESTRUCTURING AND STRATEGY
Since the acquisition of Ciba’s textiles business in July 2006, Huntsman has completed a massive restructuring.
More recently, Huntsman looked at its portfolio and initiated a complete strategy review that is now being implemented, Hulme says.
In brief, Huntsman has replaced its former business structure with just two global strategic business units (SBUs): apparel and home textiles, and specialty textiles.
“These two SBUs focus on a number of market segments where we have a clear and sustainable competitive advantage,” says Hulme.
The major tasks for a global player responsive to the market’s needs can be summarized under three broad headings, according to the division president.
First, costs have to be realistic and in line, says Hulme.
Second, he notes, product performance must be outstanding.
Third, it is vital, especially today, to achieve sustainability through optimized use of resources such as energy and water, as well as a substantial reduction of effluent.
“Huntsman’s strategy is to respond to these needs through continuous innovation,” he remarks.
Apparel markets are growing in Asia, as well as in Central America. Meanwhile, in specialty textiles, there are growth opportunities in all regions of the world, although Europe is expected to provide the highest growth.
Innovative dyes and processing chemicals are important for Huntsman because of their high water and energy-saving potential, Hulme says.
Additionally, Huntsman expects to see customers gravitate increasingly toward textile effects, so that they can offer end-users tangible life-style improvements.
“This trend will enable apparel manufacturers to differentiate their products,” Hulme explains.
ANATOMY OF A BUSINESS
Huntman’s textile chemical portfolio has six main product areas:
- Oil and water repellents, with various end uses such as apparel or technical textiles (awnings), or barrier effects for nonwoven fabrics.
- Flame retardant treatments with many end uses, such as work wear or automotive.
- UV absorbers for use in automotive and outdoor fabrics.
- Resins, fabric softeners and silicon, which offer no-iron effects, among others.
- Process chemicals for use in pretreatment or dyeing auxiliaries, to offer mills safe and worry-free production and to reduce costs.
- Fluorescent whitening agents, which provide a higher bright white level on apparel and home textile fabrics.
A global player, Huntsman’s textiles business is present in the three major regions of Asia, the Americas and Europe. Dye production is concentrated in Basel, Switzerland Mahachai, Thailand Qingdao, China and Atoto, Mexico. The company’s textile chemicals are produced in Langweid, Germany, and in Panyu, China.
To optimize its logistics chain, Huntsman has formulation and distribution centers around the globe in Pakistan, Turkey, the US, Indonesia, China and Egypt.
Huntsman’s main large competitors in textile chemicals include textile products and service provider Dystar and chemical major BASF, both German, and Swiss specialty chemical producer Clariant, says Hulme.
Huntsman also competes regionally with many chemical companies either directly or indirectly in the textile market.
“Our key advantage over these competitors is that we are global,” says Hulme. “We also have a solid technology base and are focused on bringing innovation to clearly segmented markets.”
Global News + ICIS Chemical Business (ICB)
See the full picture, with unlimited access to ICIS chemicals news across all markets and regions, plus ICB, the industry-leading magazine for the chemicals industry.
Contact us
Partnering with ICIS unlocks a vision of a future you can trust and achieve. We leverage our unrivalled network of industry experts to deliver a comprehensive market view based on independent and reliable data, insight and analytics.
Contact us to learn how we can support you as you transact today and plan for tomorrow.
READ MORE
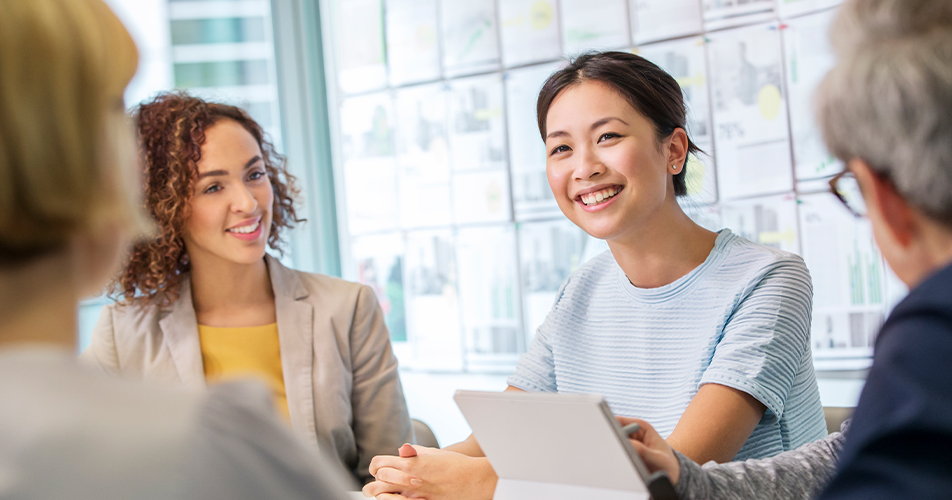