Plastics outperform metal in automotive applications
Feliza Mirasol
14-Jan-2011
As innovative plastics technologies have developed, metal car components are increasingly giving way to the lighter material
With plastic components offering advantages over metal, auto manufacturers are increasingly looking to replace metal car parts with the lighter and more economically efficient material.
|
---|
Bayer MaterialScience |
A new sunroof features an enclosed one-piece U-shaped panel made of Bayer MaterialScience’s Makrolon 2605 polycarbonate |
Exterior vehicle parts that have been replaced with plastic materials include front-end modules, beams and brackets, trunk lids, deck lids, body panels and floor panels. More plastics are being used in air-bag containers, pedals and seat components. Plastics are applied to the powertrain in the air inlet manifolds, air ducts and resonators, chain tensioners and belt pulleys, oil pans and sumps, cylinder head covers, and mechanical torsion damper components. Some gears and pump components are also becoming more plastic-friendly.
DSM ENGINEERING PLASTICS
“Plastic is a
stronger material over metal for many reasons,” says Wilfrid
Gambade, business director of Composite Resins Europe &
global markets, for Netherlands-based chemical company
DSM.
“There is higher heat resistance in friction and
oil-resistance, for example. This translates into engine
efficiency, and the engine can consume less energy to keep
itself running.”
This family of resins enables significant expansion in the use of thermoplastic body panelsV. UmamaheswaranDirector of products and marketing, SABIC Innovative Plastics, Automotive |
---|
DSM is producing thermoplastic and thermoset materials for various automotive parts in the powertrain/drive train and in the interior and exterior of vehicles.
“Plastics represent about 50% of the volume of materials used in the automotive industry, but account for only 20% of the weight,” says Gambade. “We can extend the scope for metal replacement, providing materials that deliver greater stiffness and temperature resistance – all at a lower weight than traditional metal parts.”
Thermoplastics, or engineering plastics, require intense joint development with automotive customers, says Koen Devits, business unit director at DSM Engineering Plastics Americas.
“If you summarize it, we’re talking about nylon, nylon 6, nylon 4,6, and copolyester elastomers, which are used in a wide variety of applications in automotive,” Devits explains.
“The replacement of metals by plastics in automotive has been ongoing for a long time. That’s primarily for reduction of weight of the cars, reduction of fuel consumption and reduction of emissions. Also, manufacturing processes for metal parts normally involve multiproduct steps and normally requires investment in capital. The advantage of using engineering plastics is that you have a one-step solution – you can make all the molds and parts in one shot.”
“We can extend the scope for metal replacement at a lower weight than metal parts”Wilfrid GambadeBusiness director of Composite Resins Europe & global markets, DSM |
---|
DSM has two automotive plastics portfolios. Within the thermoplastic portfolio, the company makes Stanyl PA46, Akulon PA6 (and PA66), Arnite polyethylene terephthalate (PET) polybutylene terephthalate (PBT), Arnitel thermoplastic copolyester (TPC), EcoPaXX PA410, Stanyl ForTii PA4T and Dyneema UHMWPE.
The Stanyl product group comprises high-performance polyamide 4,6, and the Akulon group 6 and 6,6 polyamides. Arnitel is a TPC and Arnite comprises PBT and PET polyesters.
Properties for these materials include extremely high heat resistance, extreme tolerance and high flowability and productivity. By comparison, the thermoset (or composite resins) portfolio houses the structural resin brands Palapreg (unsaturated polyester), Atlac (vinylester), Turane (hybrid) and Palapreg ECO P55, which is the first bio-based resin in the market with 55% biopart. The latter was launched at the automotive technology trade show SAE Detroit, as well as the composites trade show JEC Paris, both in April 2010.
DSM’s composite resins are used particularly in the development of sheet molding compounds and bulk molding compounds, which offer the advantages of part consolidation, durability, weight saving and lower capital investment.
BAYER MATERIALSCIENCE
Germany’s
Bayer MaterialScience is also developing innovative
plastics products and applications, focusing on polycarbonate
(PC) and polyurethanes (PUs).
The company’s Makrolon PC offers new styling options in the design of tailgate modules, such as developing a complete, single-part tailgate with an integrated backlite. Compared with the conventional design, where a glass window is inserted into a metal carrier, the new design involves a seamless outer skin of coated PC. This brings weight savings of 30-40% when compared with metal and glass, according to Bayer MaterialScience.
The PC is also being applied to sunroof design, specifically, a one-piece, U-shaped panel for a panoramic tilt/slide sunroof. It makes the sunroof’s glass surface appear larger while hiding the bodywork structure. This application uses black PC in a one-piece molding design without joints.
“The replacement of metals by plastics in automotive has been ongoing for a long time”Koen DevitsBusiness unit director, DSM Engineering Plastics Americas |
---|
In October 2010, Bayer MaterialScience announced the development of an innovative extra-large PC film format that can be produced using a high-pressure forming process, making it possible to manufacture large-area, three-dimensional components such as car body parts, center consoles and decorative trim as single-part components.
In the PU arena, Bayer MaterialScience has developed a new material to make very lightweight and stiff car roofs that have good thermal insulation. It developed the material through its BaySystems global PU business.
The new PU roof module has a sandwich-style support structure and would be particularly useful for battery-powered or fuel cell-powered electric vehicles and solar-powered vehicles, since its low weight per unit area (4.5kg/m²) offers weight savings.
Another innovation developed by Bayer MaterialScience and Germany’s fischer automotive systems is Direct Skinning technology, which aims to improve cost efficiency in the production of injected molded parts in a single step. Direct Skinning combines thermoplastic injection molding with the reaction injection molding (RIM) process for PU processing.
These parts require little secondary finishing, says Bayer MaterialScience. The coated component is produced on an injection-molding machine in a single mold comparable with multicomponent injection molding. After the thermoplastic substrate is manufactured, the PU system is injected into the closed mold via a PU mixing head, and the thermoplastic surface is then coated.
In January 2010, Bayer MaterialScience announced that Direct Skinning had been used for the first time with aliphatic PU in a series production of vehicle interior parts – for example, on the dashboard. The joint development produced a decorative panel now manufactured in series production.
SABIC INNOVATIVE PLASTICS
US-based
SABIC
Innovative Plastics’ portfolio includes high-performance
resins (Lexan, Noryl, Cycolac and
Geloy), polymers (crystalline, high-performance and
STAMAX), and thermoplastic LNP compounds.
The company’s latest offering launched in November 2010 – a new family of Noryl GTX resins, which are conductive blends of polyamide and modified polyphenylene ether. They cut the coefficient of thermal expansion (CTE) by 20-40% compared with previous grades, giving automotive designers more freedom to create larger high-quality, high-precision body panels than was previously possible.
This new family of resins enables significant expansion in the use of thermoplastic body panels, says V. Umamaheswaran, director of products and marketing at SABIC Innovative Plastics, Automotive.
The Noryl GTX resin has been used in the front fender of a new sports vehicle by China’s Chery Automobile. It is the first front fender made from this material and used by a Chinese automotive original equipment manufacturer. Replacing steel body panels with Noryl GTX resin has enabled Chery to cut fender weight by more than 50% (1.37kg versus 2.80kg). It also offers better low-speed impact durability. The Noryl GTX resin is also used for the fuel-filler door, a part traditionally molded and painted by the component supplier. Molding the part from the resin enables it to be painted with the rest of the vehicle body, streamlining the process and avoiding quality issues.
Japan’s Mitsubishi Motors is also using front fenders made of Noryl GTX resin in its new RVR compact crossover vehicle. Replacing steel with the resin enabled Mitsubishi to almost halve the weight of fenders in its bid to achieve best-in-class fuel efficiency.
One of SABIC Innovative Plastics’ newer areas of development is in the steering wheel, where Lexan EXL copolymer resin is used.
“We have fully validated, over the last couple of years, a complete thermoplastic steering wheel system for multiple reasons,” says Umamaheswaran. “There are weight savings compared to diecast magnesium or steel, but, more importantly, you can get almost 80% lower emissions out of injection molding versus diecasting magnesium. It is a very green solution, and we have much interest from emerging markets which may not already have the infrastructure for diecasting. This is a much easier solution to implement.”
Global News + ICIS Chemical Business (ICB)
See the full picture, with unlimited access to ICIS chemicals news across all markets and regions, plus ICB, the industry-leading magazine for the chemicals industry.
Contact us
Partnering with ICIS unlocks a vision of a future you can trust and achieve. We leverage our unrivalled network of industry experts to deliver a comprehensive market view based on independent and reliable data, insight and analytics.
Contact us to learn how we can support you as you transact today and plan for tomorrow.
READ MORE
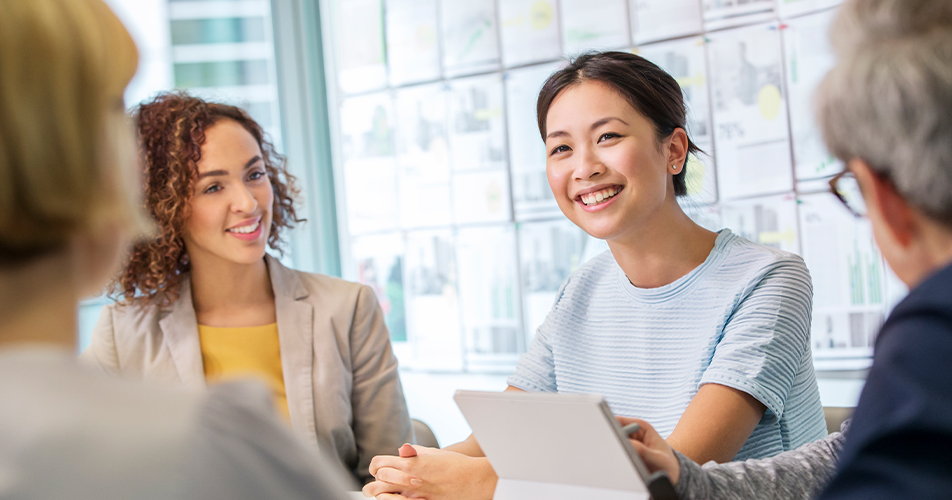