How automotives are driving demand for Asian R-PP
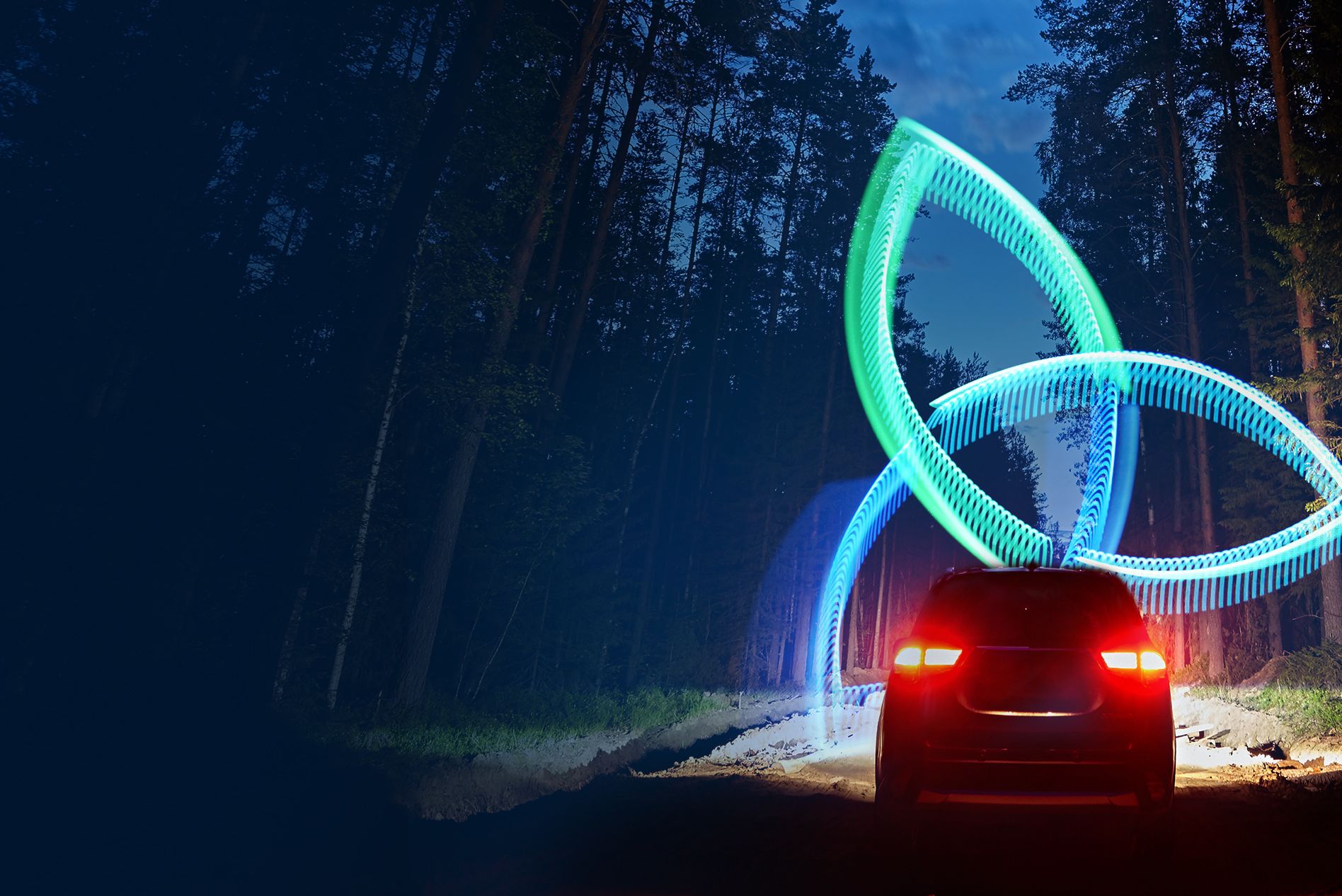
With the widespread adoption of EVs and increasing regulation relating to sustainability, automotives are increasingly joining the battle for recycled plastics.
Asia accounts for over 50% of global automotive production. China produces around a third of global output, Japan and South Korea together account for around 15% and India around 6%. Japan has had automotive recycling legislation in place since as far back as 2005, requiring vehicle owners to pay a recycling fee upfront and auto makers, dealers and dismantlers to play a role in recycling. China and India have ELV (end-of-life vehicle) legislation in place, and South Korea is considering increasing its vehicle recycling rate to 95%.
Asian automotive OEMs are taking steps to meet current or anticipated targets by increasing the use of recycled content in new vehicle models, and additionally in packaging for parts shipping and back-of-house production and transportation. Numerous collaboration projects between automotive OEMs / parts manufacturers and sellers in the waste management and recycling chain have been established in the region as a way of improving access to recycled materials.
R-PP and other recycled polymers currently used in automotives
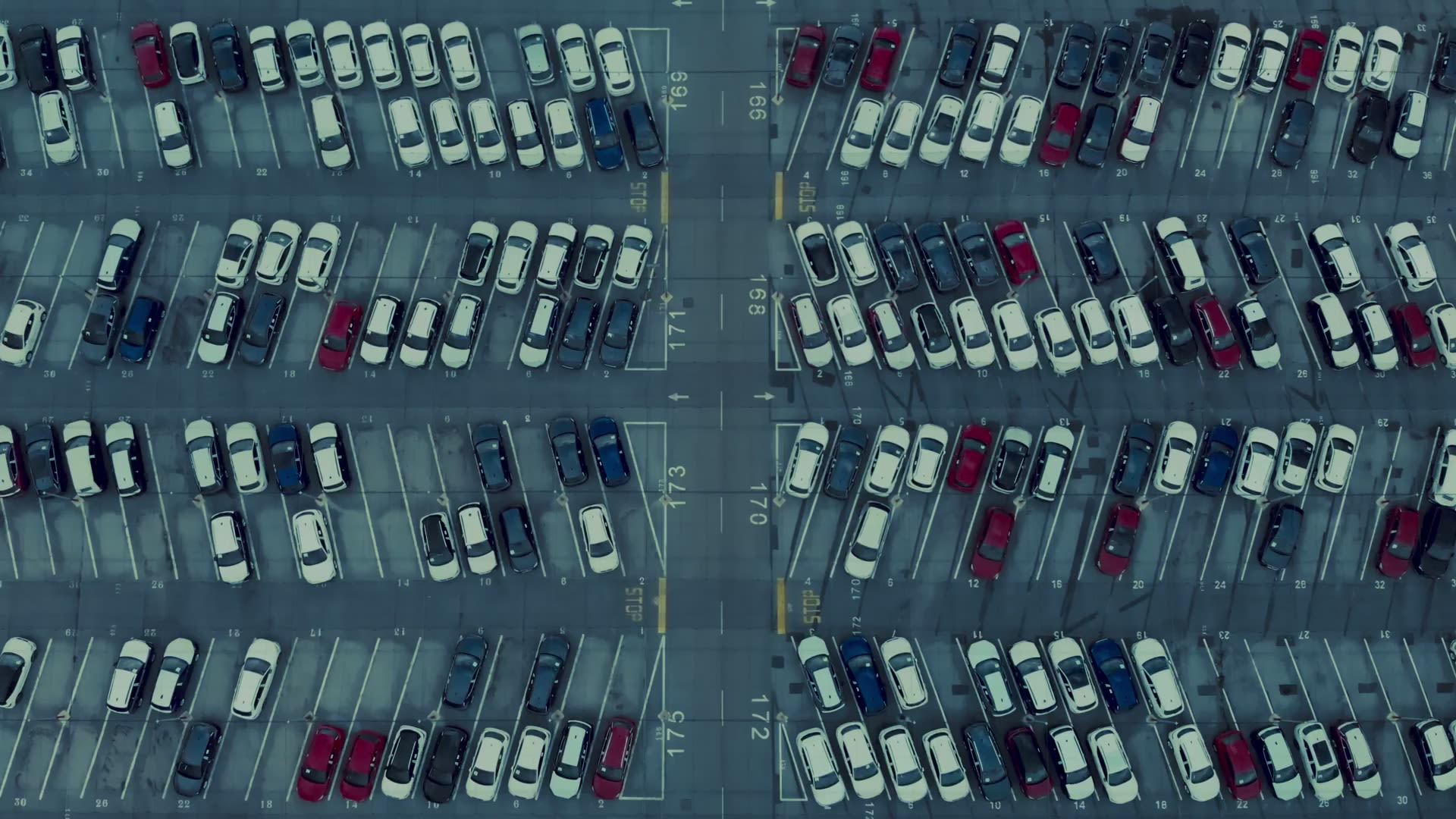
Asian automotive demand for R-PP is weighted towards premium grades
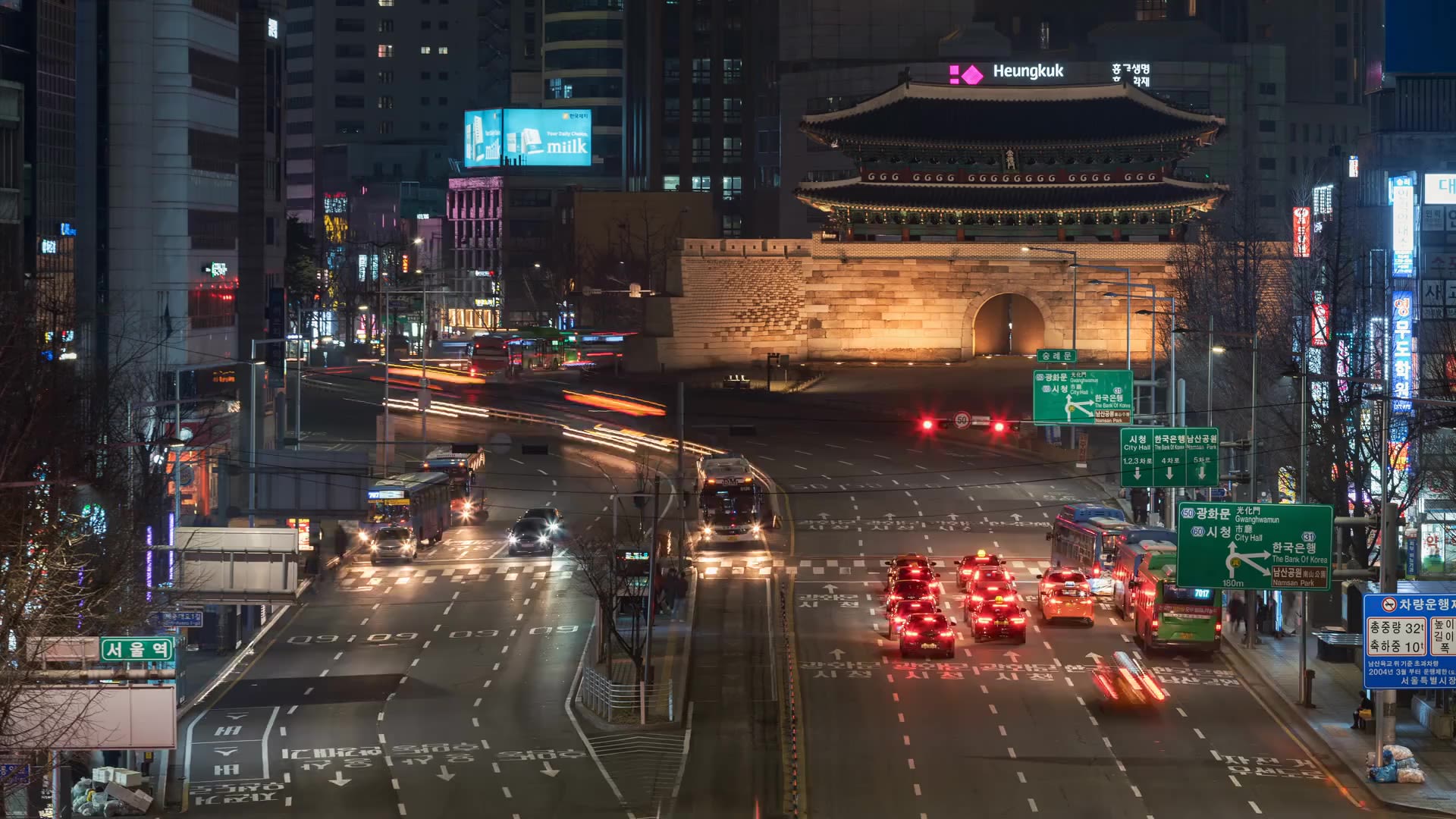
Recycled polypropylene (R-PP) is one of the most widely used recycled polymers in automotives. Of the three grades of Asian R-PP available – black, natural regular and natural premium – Asian automotive OEMs are shifting away from black R-PP towards natural regular, and increasingly natural premium grade R-PP, which comes with US FDA and other recycling certificates. US FDA is considered the gold standard in Asia for R-PP certifications.
Black R-PP is largely reserved for vehicle spare parts and after-sales services, and is priced lower than natural-coloured R-PP pellets. This growing trend will potentially impact Asian R-PP market dynamics in the future.
What impact will increased automotive demand have on Asian R-PP?
Fishing nets: the future of R-PP feedstock?
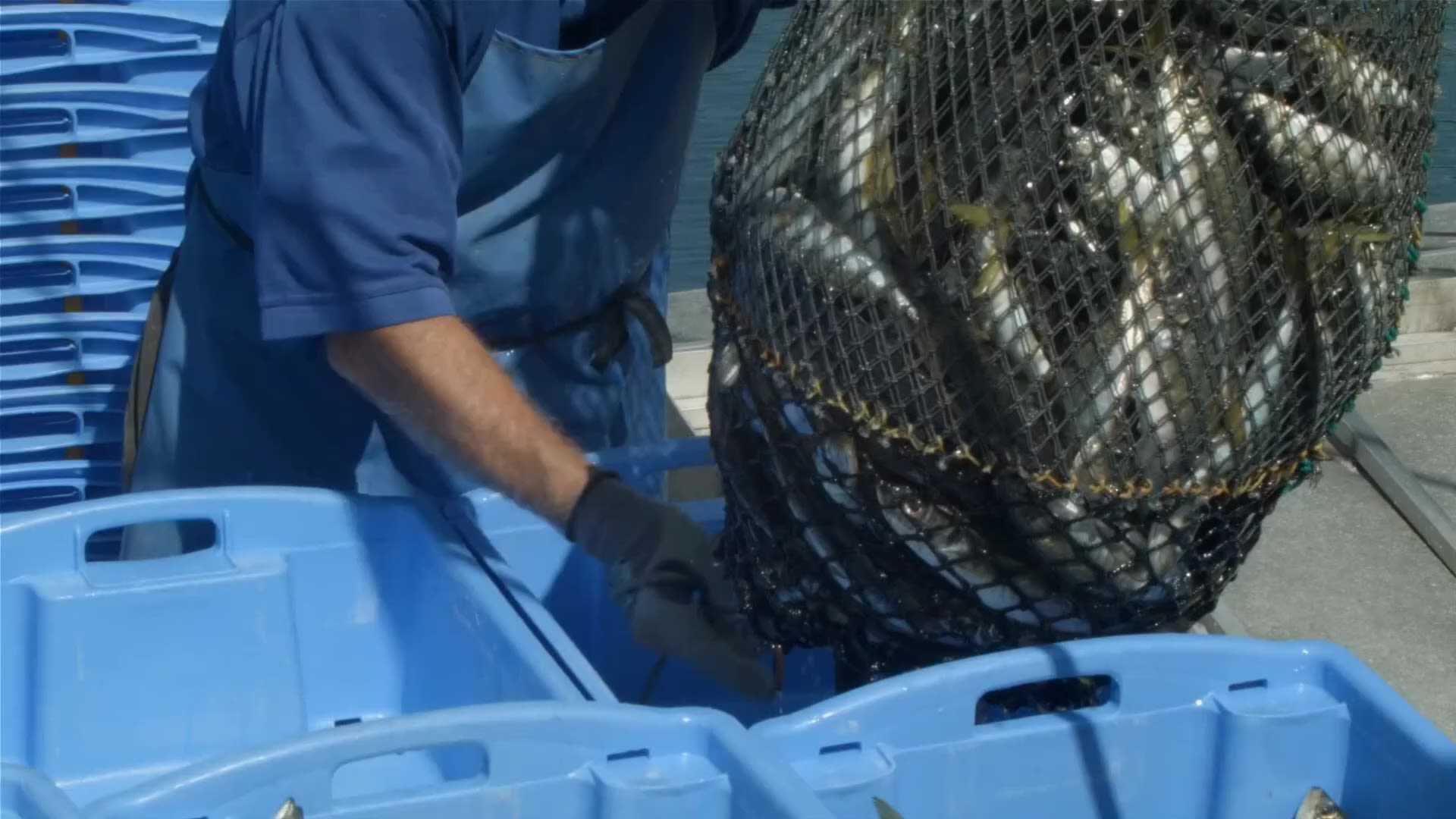
With recycled polymer supply unable to meet growing automotive demand due to limited access to quality plastic waste (especially in the case of PP and PE), both recyclers and polymer producers have begun looking elsewhere for feedstock. Companies in Southeast Asia are producing and exporting R-PP from end-of-life fishing nets. This is an attractive source of PP feedstock, being relatively easy to recycle on account of its low additive, fire retardant and functional filler content.
Major polymer producers now offer sustainable and recycled grades containing ocean plastic content sourced directly from fisheries or aggregators (small-scale waste managers that collect and pre-process/sort targeted waste).
The challenges facing automotive circularity
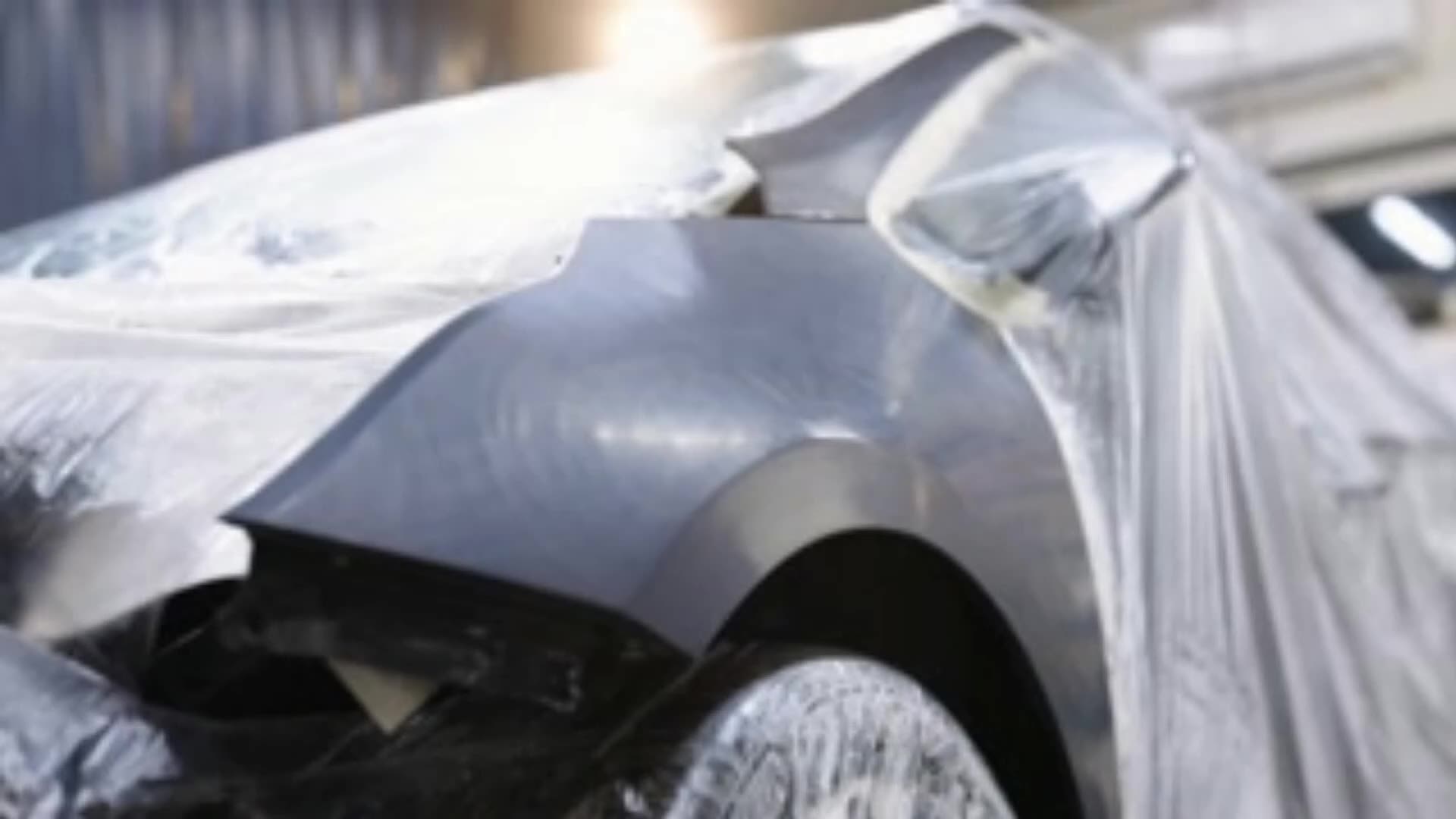
The automotive industry is working hard to achieve circularity but, in addition to a lack of access to feedstock, a range of factors make polymer circularity a significant challenge:
Conclusion
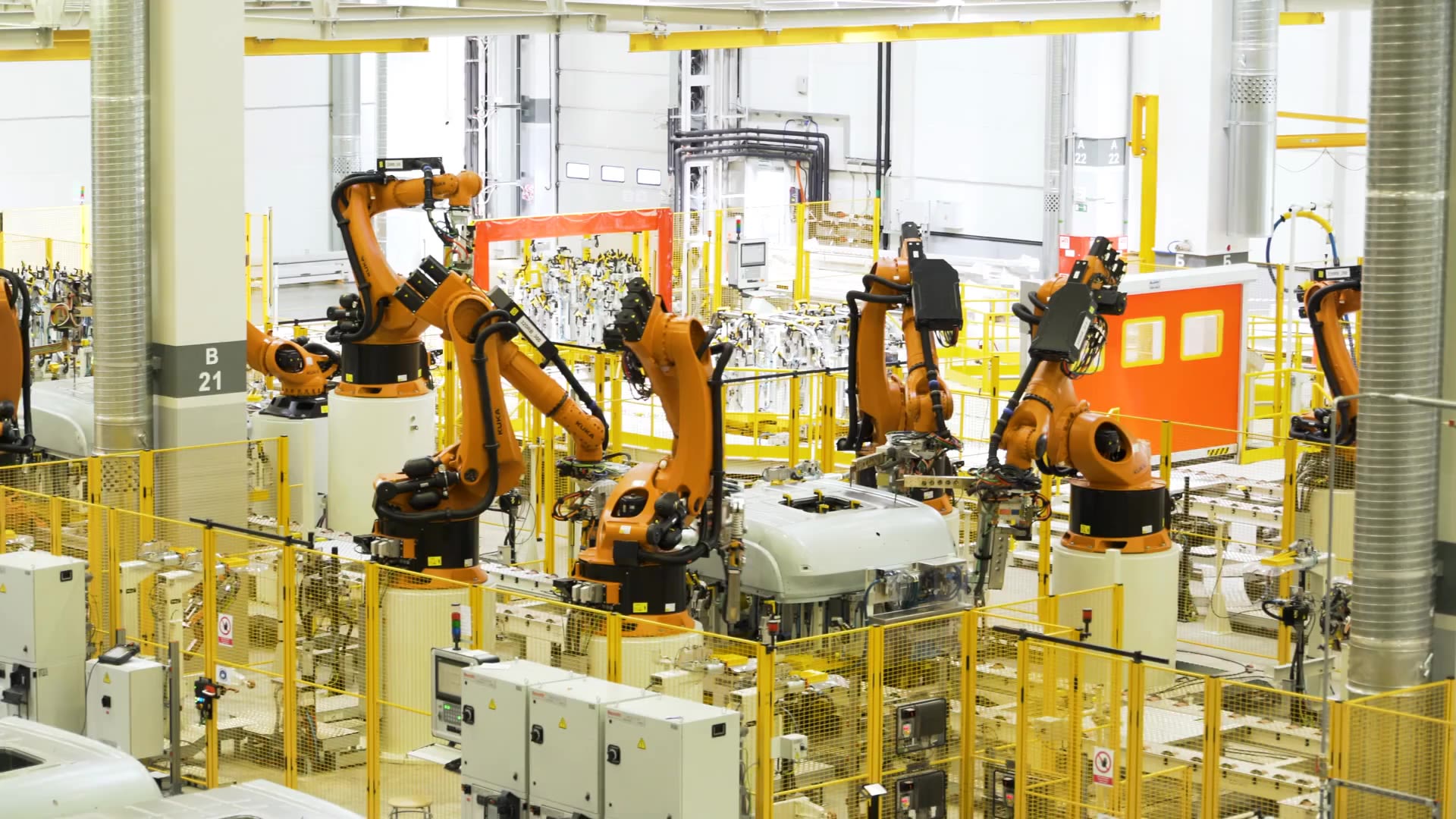
Given the importance of R-PP for automotive OEMs looking to meet sustainability objectives and / or regulatory targets, the market is likely to see continued growth. However, sourcing remains a challenge, with R-PP continuing to be the smallest recycling sector in Asia, largely due to lack of feedstock availability. By contrast, the widespread availability of PET post-consumer beverage bottles has helped R-PET become the most established recycled material worldwide, including in Asia.
Strong interest in EVs will continue to drive regulatory targets and directly bolster demand for recycled plastics including R-PP. Until the availability of recycled polymers can match that of virgin polymers, however, uncertainty is likely to continue.
To make the most of new opportunities in recycled polymers, it is vital to access comprehensive market intelligence globally for recycled polyolefins from trusted experts based within the regions. ICIS assesses more than 70 grades of R-PE and R-PP globally. Our assessments span from waste bales through to flakes and pellets, and across post-consumer, post-industrial rigid and flexible sectors, for R-HDPE, R-LDPE and R-PP, supporting sound decision making through all stages of the chain.
Author:
Corinne de Berry is a Senior Copywriter at ICIS, working across sustainability, chemicals and energy. Her interests span decarbonisation/net zero, recycling and the energy transition.
Related content
Speak with ICIS
If you are interested in learning about how our specialist insight can help you make better business decisions, contact the ICIS team today. Simply complete the form and we will get in touch with you as soon as possible.
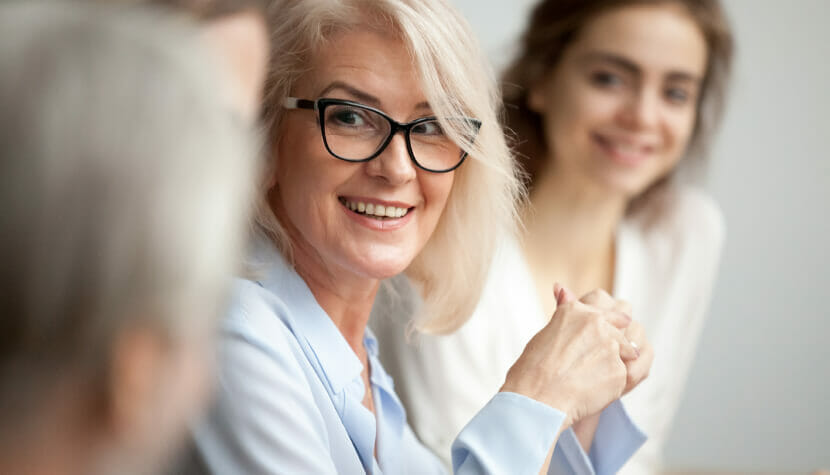